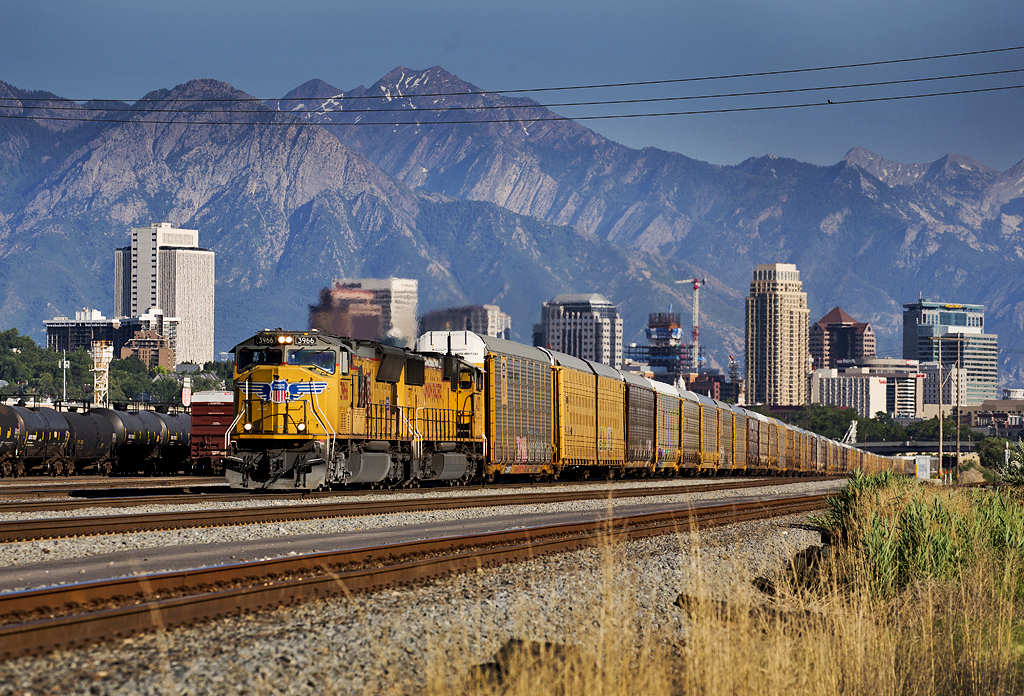
CHARLESTON, W.Va. – Consumers want to purchase new vehicles, and railroads are eager to transport them, but a persistent microchip shortage riddled with pandemic-related setbacks is likely to mean fewer auto sales and subsequently, fewer autorack loads from U.S. auto plants for the balance of 2021.
Year-to-date, U.S. railroads have transported more than 490,870 carloads of motor vehicles and parts, which represents a 5.6% increase from 2020 volumes at the same time, according to weekly rail traffic data compiled by the Association of American Railroads. On the surface, this would indicate the auto sector, and rail’s part in the supply chain, have rebounded from COVID-19 related slowdowns, but in reality, 2021’s gains are amplified by 2020’s abrupt shutdown that halted most all auto-related rail shipments in the March-May 2020 period.
Much of this year’s shipments are trailing 2020 and pre-pandemic volumes of 2019, signaling that production for semiconductors has yet to match consumer demand as the economy steadily rebounds from the pandemic. According to the AAR, U.S. railroads hauled 11,563 carloads of motor vehicles and parts for the week ending Sept. 25, which is close to a third fewer carloads compared to the same week in 2020.
General Motors delivered nearly 447,000 vehicles in the U.S. for the third quarter, down more than 218,000 vehicles from a year ago, the auto giant reported on Friday. Similarly, Nissan’s third quarter sales were down 10% to 198,955 from 221,150 vehicles in Q3 2020. And Honda reported similar third quarter results on Friday, noting a near 11% decline in car and truck sales.
As auto makers match production with the availability of the highly sought after chips, some manufacturers have idled or strategically halted production at assembly plants across the country. In early September, General Motors announced it would idle nearly all of its North American assembly plants due to the microchip shortage. And earlier in the summer, Ford temporarily halted output at its Kansas City assembly plant where the popular F-150 pickup truck is built, CNBC reported at the time.
The microchip shortage is the result of auto makers halting their orders for microchips at the initial onset of COVID-19 in early 2020. Since auto builders largely maintain just-in-time inventories, there was not an excess supply of microchips in reserve for when demand resurfaced. Simultaneously, chip-makers were trying to handle increasing demand for semiconductors used in computers and games consoles, as workers migrated to home offices. As the economy improved, overseas chip makers have had difficulty matching production with demand.
It won’t be until railroads announce their third quarter results that the industry will have a clear view on how the chip shortage is truly affecting freight carload revenues. All seven of the Class I railroads highlighted double and even triple-digit percentage increases for automotive shipments in 2021’s second quarter, but again, those numbers were largely inflated by 2020’s production halt during the worst of the pandemic. Traditionally, BNSF Railway, Union Pacific, CSX Transportation, and Norfolk Southern have been the biggest players in moving automotive shipments. UP alone moved 173,000 automotive carloads in 2021’s second quarter ending June 30. In the East, NS moved more than 82,300 carloads and CSX at 77,000 carloads. For CSX and NS, that was a 120% and 122% volume increase, respectively.
In the coming weeks, updated quarterly revenues will be distributed, providing better guidance on how the availability of semiconductors is really impacting automotive shipment revenues on the U.S. rail system.
You have to blame the politicians and big corperations in this case for the chip shortage why, what happened to (MADE IN AMERICA). Products made out of this country has gotten way out of hand America use to be the prime manufacturer of everything needed for Americas and the world , until big Companys got greedy and the higher ups wanted more money in their own pockets . The CHIP for the autos and a lot of the products that are short handed in the stores should all be brought back and made in the good old U.S.A. not CHINA or KOREA , Americans would have great jobs and the economy would be on fire simply put . MADE IN AMERICA lets bring back that label again people !!!
Haven’t seen any slowdowns from the BMW plant in Spartanburg SC.NS train 18D runs 6 days a week with anywhere from 80 to 95 loaded auto racks to the Port of Charleston.
There were two silicon fab that had major problems last year. One was totally destroyed and the other was shut down several months for repairs. The impact of the events was hidden by the slowdown in silicon demand due to the pandemic. As silicon demand has returned, some silicon has been in short supply. This has caused part of the problem. Other materials for manufacturing have been reported to be hard to get and expensive.
Another problem has been the transportation industry. The news has reported ships sitting three weeks awaiting a berth to unload containers, no chassis available to haul containers and no labor available to move containers over the highway.
As the industries have moved to “Just in Time” (or Just in Trouble) production to minimize capital in inventories, they increased their exposure to difficulties outside their control.
I would say the frustrating part in all of this is that suppliers and producers are cashing in whether it be the chipmakers who held off on capital investment and now are naming their prices to the latest oil price increase driven in part of by Saudi’s, Russians and US Fracker’s cashing in instead of turning on the spicket.
…
Or maybe, just in general corporate mentality of putting shareholders in front of the line and capital or even workforce investment a distance third or fourth or fifth. Sounds Familiar? So kinda of ironic Railroads are not put of the recieving end of things.
This is a consequence of the automakers making computers on four wheels, instead of cars and trucks any more.
yep, big part of it.
Most of the shortage has to do with the increased demand for cars. The plants cannot ramp up quickly as the entire supply chain takes months to fill up. Also last years stimulus money fed the demand for vehicles (you can only eat so much). These numbers will not mean much for the next few years.
@ Noel Petit Huh? Numbers do not mean much? Respectfully, I found the first part of your comments to be informative but the last part puzzling. The numbers and article content suggest a lot of lost wages and spending power from factory floor to railroad and trucking to show room floor. Thus a significant drag on the economy and extra pain in many peoples’ and communities lives. With changes in commuting habits, shopping habits and interest in driving by younger generations, these may be losses that are never made up– granted this last point is a bit beyond the scope of the article itself.
Just passed my local Chev. dealer an hour ago. there’s no more than twenty new vehicles on his lot. There was always close to two hundred. guess it’s not time to go shopping for a new pick-up.
Our nearby Subaru showroom has turned into a snack bar. Cars are sold before they leave the factories in Japan and Indiana. I didn’t check the adjacent Jeep/ Dodge/ Chrysler showroom so I can’t say.
This is why year to year statistics aren’t a good indication of long term trends.
Who would have thought demand for video games would draw down supply of autos?
Actually, video games use more modern silicon. It’s the propensity of automakers to use legacy silicon that most fabs left the market years ago. The margins for chipmakers to bring up their fabs just to make old chips are low and because automakers are too lazy to certify newer ones is what is driving the “shortage”.
CPU’s, memory and other high performance silicon used in daily computing are down to 14nm or less. Automakers are still using chips that use 32nm and 36nm designs, a market long left behind. Global Foundries has several US fabs and even they are at 22nm and they are considered the slacker of the bunch.
Many in the auto supply business are getting pretty weary of their propensity to wait until the last minute to make their supply orders known and only to find its more of the old stuff. The equipment to make such old stuff is getting old and more expensive to maintain, but Auto USA wants bottom dollar.
Intel CEO Pat Geslinger gave the automakers a good scolding at a meeting in Germany last month about their poor silicon buying habits. With the fabrication industry going through a huge effort to dis-integrate their vertical production stack, now is a good time for Auto USA to get more advanced procurement methods and get into the current century.
If they keep treating chips like a rubber hose from Gates, then this will keep happening.
I have read elsewhere that this is the main cause , but thanks for all the details.