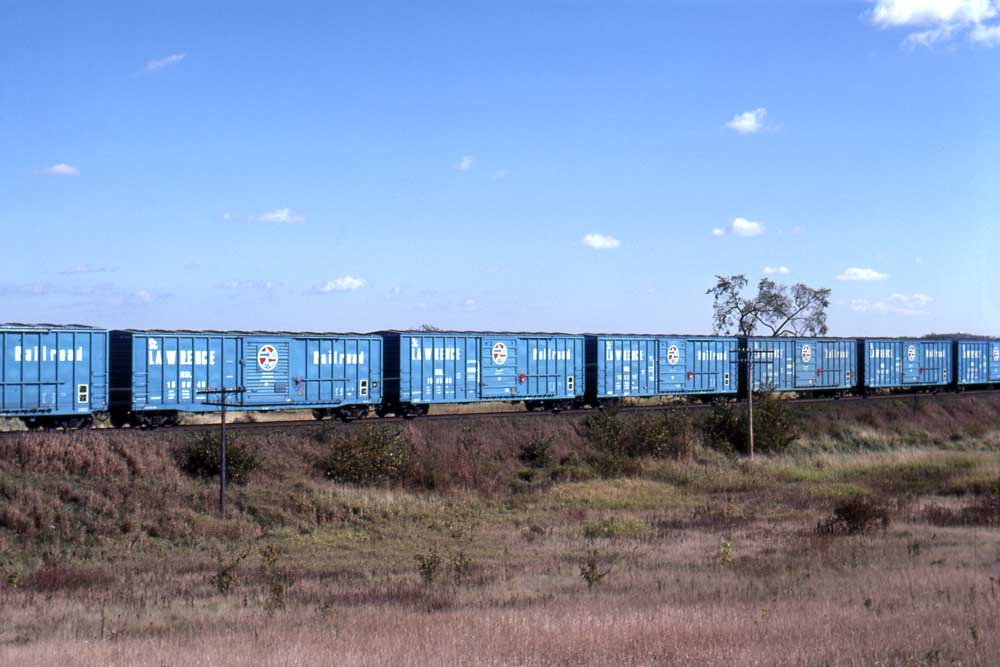
WASHINGTON — The Railway Supply Institute, the trade group representing the companies that build and lease freight cars, today asked federal regulators to take action that would prevent the North American boxcar fleet from hurtling over a looming retirement cliff.
The problem: Boxcars are being scrapped at a faster rate than they are being built. The trend is expected to accelerate, with 22% of the current boxcar fleet set to age out by 2030, which would create a shortage of boxcars and shift freight to trucks.
The culprit, RSI says, is the 1994 car-hire Arbitration Rule, which keeps boxcar leasing rates artificially low and therefore reduces incentives for new construction. The default rate, as low as 17 cents per hour for a boxcar that costs more than $150,000 to build, has been stagnant for decades.
“America is plunging toward a boxcar cliff as many cars are hitting their 50-year expiration date and not being replaced because the Arbitration Rule suppresses boxcar rates far below competitive levels,” RSI President Patty Long said in a statement. “The current car hire system discourages investment in this integral component of our rail transportation fleet, with boxcars providing efficient shipping for crucial American commodities. We can’t afford to fall off the boxcar cliff. Reform is needed now.”
In a filing today, RSI has asked the Surface Transportation Board to review the Arbitration Rule. After receiving comments on RSI’s petition, the board will determine whether to reopen the Interstate Commerce Commission’s Arbitration Rule decision and solicit comments on whether to condition or terminate the approval.
The Arbitration Rule includes a provision allowing the Association of American Railroads’ Equipment Assets Committee to consider and vote on amendments to the rule. TTX, which is owned by the Class I railroads, is exempt from the Arbitration Rule.
The AAR panel has no incentive to revise the Arbitration Rule, RSI says, because changes would allow investors in railroad boxcars to compete on relatively equal footing with TTX.
RSI in 2019 proposed changes to the Arbitration Rule, but the Equipment Assets Committee rejected the measure.
Not everyone agrees a boxcar shortage is looming.
TTX says the ratio of fleet size to loads has remained the same due to declines in the number of boxcars and boxcar loads, and therefore no rule changes are necessary.
High-capacity boxcars are replacing old, lower-capacity cars, meaning that the industry does not have to replace retiring cars on a one-for-one basis, TTX says.
In the past two decades, boxcar loads have declined by 44%, according to RSI, while the fleet has shrunk by 39% since 2008.
Recall a major class 1 rail carrier “sales executive” referring to interchanged, short line boxcar business as “loose car” railroading. If the “sales folks” felt that way, guess what the operating team felt!
Handling boxcars costs money, which in turn increases ORs. Ancora was very clear they wanted to jettison high cost rail traffic, e.g., single car shipments. That does not look good for the boxcar user as Mr. Sutherland notes.
Ancora also wants to eliminate low margin shipments such as intermodal. That throws ice onto Mr. Saunders’. idea.
An old SP Conductor once groused that there was a tried and true method of getting freight over Donner Pass after Ed Moyer started pulling up track, “Wagon Trains!” (Ed Moyers was EHH’s mentor at IC.)
Sounds like the traditional boxcar needs a modern update. I am surprised they haven’t moved to a single door, roller floor design like airlines use in their freight fleets.
Then you can use a standard freight container size that allows micro-mixing of freight in a single secured boxcar. This also allows for robotic loading and unloading using a roller ramp. Bar code scanning the containers allow automation in routing at the yard to its dray.
I would think that the days that InBev Budweiser or Miller Coors would load up boxes of canned beer in a old boxcar, just to have yard thieves snag them in the middle of the night is over.
I blame the irresponsible, reckless class I’s. Many shippers still prefer the 50 foot box (multi-plate) as they refuse to pay the cost of transitioning to larger bay doors. I feel terrible for the short lines who know how to fill box cars and other loads. They are at the whims of the clueless Class I’s and associated numb-skull, activist owners.
Why don’t they just take all the excess containers around, cut doors in the sides and farm them out to companies that would load to destination on a schedule and they could put the containers in spine cars and problem solved. Most people who need a boxcar, outside of paper mills, grain mills and some other miscellaneous bulk products, hardly ever have a full load so combining loads for a discount to a certain break point to offset the slightly lower delivery times could be a way of using up all the stray containers covering the country side and back alleys around cities, as well as making these loads more enticing to the railroads to move…
The high volume boxcars are indeed more efficient, but only if the shipper has enough product going to a single destination to actually use them to advantage. Consider that containers often hold not much more than a more traditional sized boxcar and are very popular, simply because they can go their separate ways.
I feel a major reason boxcar loads are decreasing is that the big railroads are doing their best to discourage them. Handling that type of business requires a little more management effort and they have become lazy. Consider how many short lines have been able to increase business by simply trying, even if those efforts can get sabotaged as soon as the traffic reaches the Class 1 in interchange.
Well said. I agree.
The only reason boxcar loads are decreasing is because railroads don’t know how to handle traffic in boxcars, nor do they have the proper size to price metrics. It’s 2024, all new boxcars should be 63 – 67 foot high cubes, no exceptions. Cubic capacity should be at least twice that of a 53 OTR trailer, so you could ship two loads for one at…cost wise I’d say 1.5 times the price of one OTR move. The other problems is receivers and shippers are not being served directly by rail anymore so you have to involve transloading facilities, adding in extra costs. That’s just pore decision making though on the part of manufacturers, warehouses and retailers.