As the postwar era began for Lionel, concern for a more colorful, more highly decorative product was paramount, so Lionel examined different processes for decorating their trains.
The tried and true methods (heat stamping and rubber stamping) were used to great success, but both had limitations. With heat stamping, a fairly flat surface was needed, and only one color could be printed at a time. Although superior to other processes available at the time, these limitations meant more hours for labor, and the need for a higher priced product if the decoration required was complex.
Rubber stamping, (or more accurately, wet-on-wet offset printing using a rubber pad) had the advantage of printing up to three colors in one pass, but the results weren’t always crisp. Image registration (the correct line-up of the different colors) was often imprecise, and examples of stamped items surface that never should have made it past quality control.
Modern pad printing, the method used for decorating the majority of items including almost all modern era trains, had not been invented in the 1950s.
Lionel did make limited use of screen printing, or as it was known in the 1950s, silk screening (the screen mesh was made from silk). Silk screening required a technically competent, professional printer. Also, the screens from the 1950s had a tendency to break down or leak after only a few hundred passes, often causing blurring, so results weren’t always top notch.
Screen printing also had the disadvantage of slow-drying, solvent based inks which often attracted dust particles as it dried, and like heat stamping, only one color could be printed at time. An absolutely flat surface was required for screen printing, and raised relief designs in body molds like rivets, ladders, and louvers contributed greatly to early breakdown of the screens, and consequent image blurring.
Since Lionel’s production runs often ran into the tens of thousands, they quickly found that silk screening was not a cost-effective method. Still, Lionel used it for a few items, (probably where other methods would not work as well) until 1957, when they discontinued the practice.
The highly complex paint schemes of the streamlined diesels that were popular in the late 1940s and 50s forced Lionel to make use of another tried and true decorating technique — decals — for those areas where printing and stamping could not be used. Since most decals contained a complete, sharp, often four and five color design, the final decoration could be applied by a non-technical factory worker with a roll of paper towels and a dish of water.
Yes, that’s exactly how those Santa Fe, Canadian Pacifics, Rio Grandes, Milwaukee Roads, and dozens of other models were completed. Those decals were applied at the Lionel factory the same way you would at home. Certainly all of us have observed a factory original Lionel item with the decal placed crookedly. Don’t always blame the employees; a decal can slip if the item is packed before it has completely dried.
History of decals
Decals have been around for a long time. The full name for decals is actually “decalcomania.” The term comes from combining two French words meaning “to trace” and “the art of imitating porcelain ware.”
A design is printed on a special water-sensitive paper and coated with a clear carrier film to contain the design and allow it to transfer to the intended object. When immersed in water, the entire design and carrier film slips off the transfer paper and can be placed wherever desired. Decals are delicate, thin and prone to tearing and rupture at this stage.
For Lionel, probably the most famous water decals were the lettering and numbering sets they made for the 1937 “700K,” or kit-form scale Hudson. One complete set of engine numbers “5344” and tender lettering “New York Central” were supplied with each set. (Normal production 700Es were lettered in silver using rubber stamping.)
How decals are made
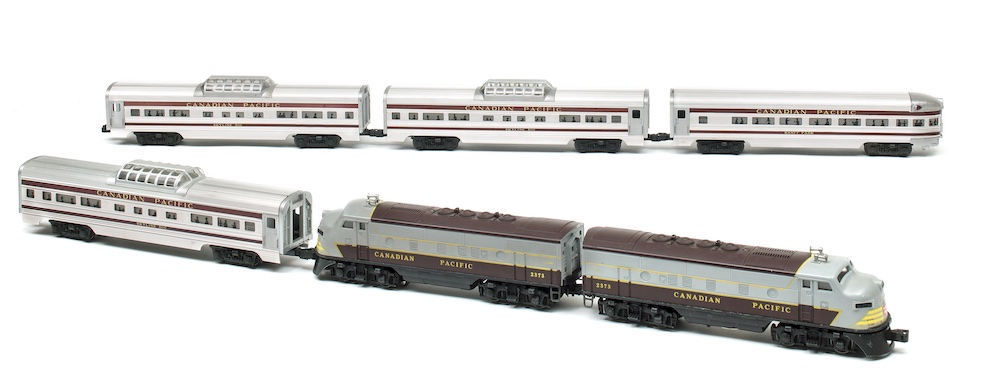
Decals are manufactured most often by screen printing on the special transfer paper. Unique decal lacquer inks are used, and the decals are printed one color at a time, although decal sheets may contain as many as 100 or more complete decals. Quite often the clear “carrier” film is printed as both a base coat, and also as a top overcoat to “seal” the colors for both strengthened durability, as well as to prevent fading of the light sensitive colors. Unfortunately, over time, the clear lacquer coat, like most lacquers and shellacs, yellows or oxidizes with age, creating an amber-like halo around the decal design; this yellowing or ambering is the most positive method to identify an original Lionel decal.
The inks used to create decals today are not quite as light-sensitive as their 1950s counterparts, so recent manufacture decals should not exhibit the vast discoloration of their earlier cousins. I should point out that while some decal manufacturers will try to artificially “yellow” their decals, to give them a more vintage look, when compared to an original, the difference is most obvious. If you carry around a small, original “ambered” decal with you, just compare it to any non-original aftermarket decal; you’ll easily see the difference on most any item.
Amberization/discoloring is not the same with every original Lionel decal; some are slightly yellowed; others may look like they’ve been bathed in rust. The differences come from factors such as storage, temperature, humidity, exposure to heat, light and air, and other environmental factors.
Decal disadvantages
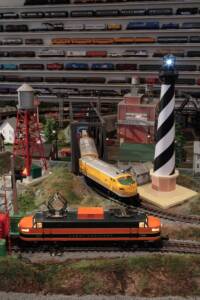
There are two disadvantages to water decals: They are fragile. When placed over irregular surfaces, over time they will flake and peel, leaving a tattered and damaged look to an item. Notorious among the postwar Lionel catalog are the No. 2358 Great Northern EP5, whose large nose decals often react to the orange paint underneath; and the 2373, 2378, and 2379 Canadian Pacific, Milwaukee Road, and Rio Grande F3s, which are often found with the decal image lost by the front nose louvers, leaving an incomplete decoration image. In 1970, Lionel MPC solved this problem by eliminating the nose louver detail entirely from the mold.
Secondly, the decal carrier film leaves an unsightly halo around the entire image and has an unfortunate tendency to yellow with age. In some instances, like the No. 2373 Canadian Pacific, where large sections of the decal are held together by the carrier, the entire front of the locomotive can appear completely discolored. Although this usually will not affect the investment quality of the piece, provided the decal is not broken, it looks awful.
An unusual “decal” variation
The only variation from water release decals in Lionel’s postwar catalog that I’m aware of is the No. 2350 New Haven electric. The nose graphic on this particular diesel was complex, and Lionel originally tried inking the detail on, while rubber stamping the “NH” graphic. Results were spotty, rejection rate was high, and Lionel was faced with a real problem. As most collectors know, factory “painted nose” New Havens are highly desirable.
The factory was having serious production problems with this engine, and eventually solved them by resorting to a pressure sensitive cellophane transfer (not, strictly speaking, a decal). Two of these unique transfers were pasted across the double ended noses of the most common version of every 2350 electric. Why they chose this pressure sensitive transfer as opposed to the tried and true water decal is beyond me.
Curiously, the No. 209 Alco New Haven with almost identical nose graphics did make use of a water decal. Original 2350 NH decals are prone to the same shortcomings as water release decals (the paint often flakes). However, the cellophane backing does not, and 2350 NHs are often found with high paint loss and what looks like adhesive tape underneath.
Decal manufacturers
In the 1950’s, Lionel did not manufacture their decals in house; they purchased them from several manufacturers in the U.S. My guess for this reasoning is that their orders were huge; maybe one manufacturer couldn’t keep them supplied on a timely basis.
The general consensus among historians is that at their peak, Lionel was producing 120 Santa Fe F3 sets in an hour! In two 8-hour shifts, they’d produce 1,920 engines a day or 11,520 a week (given a six day work week) or 46,080 a month times the four month peak manufacturing season, or approximately 184,320 Santa Fes a year. Each No. 2343 AA set used six decals – four “GMs” and two Santa Fe nose decals, meaning that for one model in their catalog they required 1,105,920 decals per year. That’s a pretty tall order!
Some of the manufacturers Lionel contracted were American Decalcomania Co., New York; Chicago Decal Co., Chicago, Ill.; Meyercord Co., Chicago, Ill.; and Palm Bros, Cincinnati, Ohio.
Lionel’s decals were ingenious, and did exactly what was asked of them, solving the complex decoration problems of the 1950s.
BONUS: Download a chart of Lionel postwar locomotives with decals!