Track buses for Digital Command Control: Layouts wired for direct-current block control have several isolated track sections called blocks. Each block has an electrical switch that controls which DC throttle powers that track section. In theory, a Digital Command Control (DCC) layout could be wired as one large block with two wires feeding the power directly from the DCC booster to the track. However, on any model railroad larger than a test track, more wiring is necessary if you want your trains to run well.
Since DCC can power more than one locomotive at a time, more current is required to pass through the rails than with DC control. Small DCC systems usually have boosters that can supply at least 3 amps. Bigger systems can supply 5 amps, and large scale model railroads use boosters that can supply 10 amps. In DCC the voltage remains constant, and each locomotive draws as much current as it needs at the time. A train going up a grade draws more current than a locomotive running by itself on level track. Locomotives in larger scales draw more current than those in smaller scales. The sum of all the current to each locomotive is what the DCC booster supplies. A medium sized HO layout with just a few trains with three locomotives each can approach the capacity of a single 5 amp booster.
So how do you get the current to the trains? Nickel silver rail is a poor conductor of electricity and acts like a resistor. The longer the rail, the more resistance there is. Following Ohm’s Law, the more current going though a resistor, the larger the voltage drop from the booster to the locomotive.
I measured a piece of code 83 nickel silver rail and found the voltage drop was .057Ω per foot. That doesn’t sound like much, but on anything but the smallest layout, it adds up quickly. At a full 5 amps, one piece of 3-foot flextrack fed at one end can cause a voltage drop of 1.7 volts at the other. How? Because the current must travel three feet down one rail, pass through the locomotive, and return three feet down the other rail. Imagine what it would be like on the other side of a large model railroad.
Feeding a layout with only two wires may not only affect locomotive performance, but it could be destructive. Since DCC boosters can supply more current than a typical DC throttle, they’re equipped with internal circuit breakers that trip and remove power from the rails when a short circuit occurs. If not wired properly, the voltage drop through the rails may be so great that the booster isn’t able to detect a short. The full current capacity of the booster passing through whatever is causing the short can be destructive enough to melt a brass truck frame.
Fortunately, copper wire has a much lower resistance than nickel silver rail. The solution to the voltage drop problem is to run a track bus of heavy gauge copper wire beneath the layout, roughly parallel to the track, and smaller gauge track feeders from the bus to the rails. The size of the wire required depends on the length of run and the capacity of your booster. There’s no set maximum voltage drop that’s acceptable, but it has to be low enough so that the booster circuit breaker trips when a short occurs.
Each DCC manufacturer has different recommendations for acceptable wire size and length of wire runs. Different boosters may detect short circuits at different levels of voltage drop. It’s important that the wiring is capable of handling the current output of the booster and that the booster circuit breaker will trip.
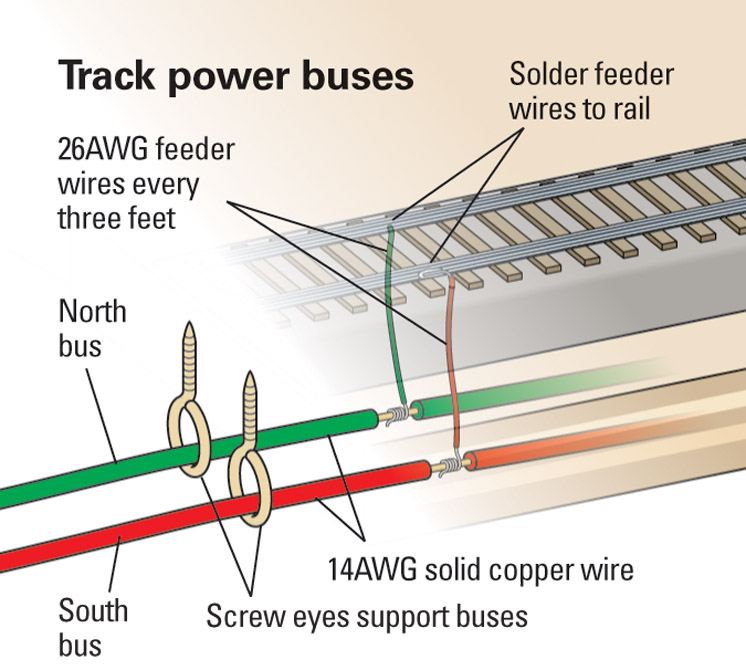
For boosters that supply 5 amps and less, 14AWG for runs of less than 30 feet is fine. If you have a longer run or larger booster, consider using 12AWG or larger. You can determine the worst-case voltage drop by multiplying the wire resistance by your booster’s full current capacity. There is a handy calculator for this online at www.cirris.com/testing/resistance/wire.html. Enter the length of the run and bus wire size to determine the wire resistance. Remember to double the value to account for the voltage to the locomotive and the return.
There is a debate about whether solid or stranded wire is better for track buses. Either one will work. Digital Command Control is an AC waveform, so skin effect (AC flowing only through the outer layer of a conductor) will cause a slightly larger voltage drop in solid wire, but not enough to make a difference.
It’s important to color code your bus wires to make sure that the same bus wire goes to the same rail throughout the layout. I use red for one rail and black for the other rail. From the track bus, smaller gauge track feeders carry the current to the rail. I use 22AWG on my HO layout. This would be impractical for an N scale model railroad. For short runs between the bus and the rail, the gauge of the track feeder isn’t as important as the track bus gauge. Good electrical and mechanical contact to the rail is what’s important.
Nickel silver rail is a poor conductor, but rail joiners are worse. Over time they will loosen and the rail will oxidize. It’s a good idea to use feeders for every piece of rail and solder rail joints on short
sections of rail.
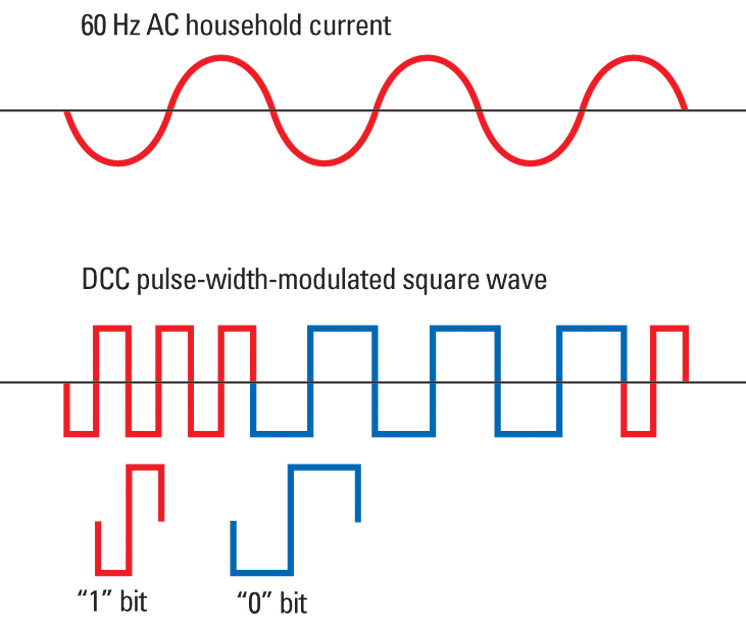
Digital Command Control signals are square waves, and consequently generate a lot of noise at all sorts of frequencies. This can cause interference with a number of electronic devices, including your DCC throttles through the DCC cab bus. Though not a hard and fast rule, the track bus should be routed a foot or so away from the cab bus.
Another way to cut down on interference is to twist the bus a few times per every foot or so. Don’t twist the bus so much that it is difficult to attach the feeders. Twisting the bus also has the effect of increasing the DCC signal fidelity. At the end of long buses, the square wave of the DCC signal can become distorted and cause excessive voltage that could potentially damage a decoder. NCE Corp. suggests placing a snubber at the end of a long bus. Digitrax doesn’t recommend using a snubber on its system.
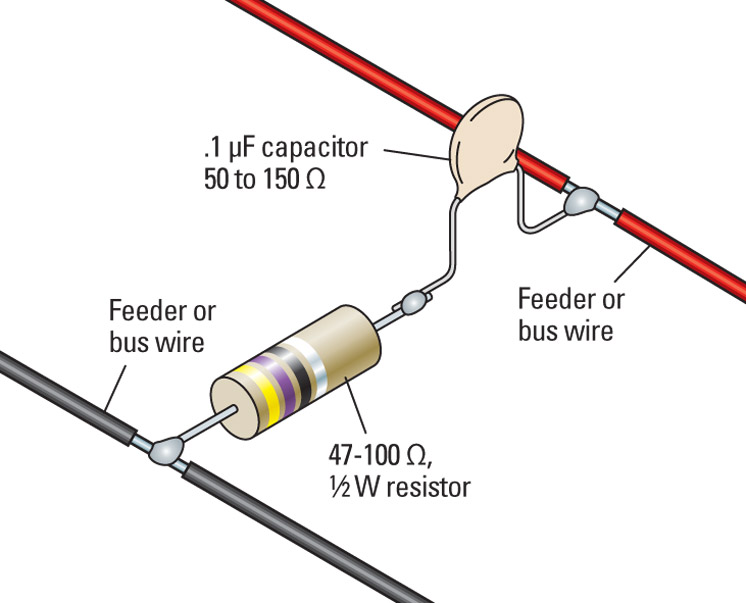
As you wire your layout, frequently test your work by shorting the rails together at different locations. Your DCC booster should shut down. If it doesn’t, check to make sure you have enough track feeders. Dividing your track bus (and the track above it) into electrically isolated sections that are powered by additional boosters or protected by DCC circuit breakers will make it easier to diagnose short circuits.
For the snubber, it doesn’t matter in what direction you connect it between the bus wires. The resistor has no polarity, so it makes no difference which end is connected to the capacitor and which is connected to the bus. The capacitor will most likely be a ceramic type, usually in the shape of a wafer, which has no polarity and large voltage range, and would be safe to use in either direction; however, if you were to use an electrolytic or other type, it does have a direction and is sensitive to polarity (a positive or negative symbol is usually printed on the can over the appropriate lead wire) and voltage – avoid using them for this purpose, unless you validate their use with an electrical engineer or designer, or risk damaging them due to the reversing polarity of the DCC signal and present a surprising fireworks display.
I’m just starting/planning a HO scale layout, my room square footage isn’t really big 10′ x 12′ luckily my wife gave me permission to use all of it. I’m leaning toward a NCE DCC system and I’ve designed my DCC controller/power booster off set from the middle of my U shape design and planning on running a bus out to both ends. I’m thinking of using 14 AWG romex (house wiring) for my main bus (will remove conductors from casing). Does anyone think that may be a mistake. Also since my layout isn’t very large, will I still need to place a shunt on one or both ends?
Thanks Vance!
I have already purchased 16 AWG wire for my N scale layout to handle the bus line and was planning to buy 20 AWG for the feeders. Since your article recommends 22AWG for the power bus wires and your illustration (fig.1) shows 14AWG and 26AWG respectfully,is this OK?
As quoted from your DCC article, “(I) use 22AWG on my HO layout. This would be impractical for an N scale model railroad.” I’m building my “late-in-life” N-scale model train layout and wondered why it would be impractical to use 22AWG for my N scale model railroad?
The only thing making 22 ga. wire impractical for N gauge is the size. @@ ga wire is almost the same size as the rail. Therefore, hard to conceal.
Not so much of a comment, as rather a question. Am I reading this article correctly? Are separate buss wires required for track power and DCC signal, or is one buss used to carry both? Obviously I’m new at this.
Why is 22-Gauge drop wire impractical for N-Gauge? Why gauge is practical?
No, it shouldn't make any difference,
Does it matter which direction the resistor and capacitor go?
Figure 3 is in error. The RC network is an AC termination for a transmission line and should be placed at the END of the bus to terminate it and eliminate voltage reflections. Thes reflections are additive and could destroy a decoder. The capacitor should be a ceramic capacitor with low inductance. It doesn't function as a filter or a snubber but as a bus terminator.
Twisting the wires does two things: it minimizes external electrical interference and it controls the characteristic impedance of the bus. A change in the characteristic impedance could cause a voltage reflection. A consideration in high speed systems. Generally, a slight impedance change is not a problem in DCC systems. If you plan to use signaling, I'd recommend parallel untwisted wires to minimize any problems with the signal circuits.
Twisting bus wires together, as explained in the article, may reduce interference with other electronic equipment. On the other hand, running them parallel makes soldering your drops to the bus much easier. (If you go the twisting route, be extra careful to solder the left and right rail drops to the correct color bus, or a short will absolutely occur! Try using color coded drop wires. Also, if you stagger your solder joints by at least two inches, you should be able to avoid taping each joint.)
I've been told that the bus wires should be twisted together rather than spaced apart in parallel. What is your position on this, and if you agree, what is the advantage?
Any thoughts as to why Digitrax does not recommend these snubbers? I have both and experience no problems.