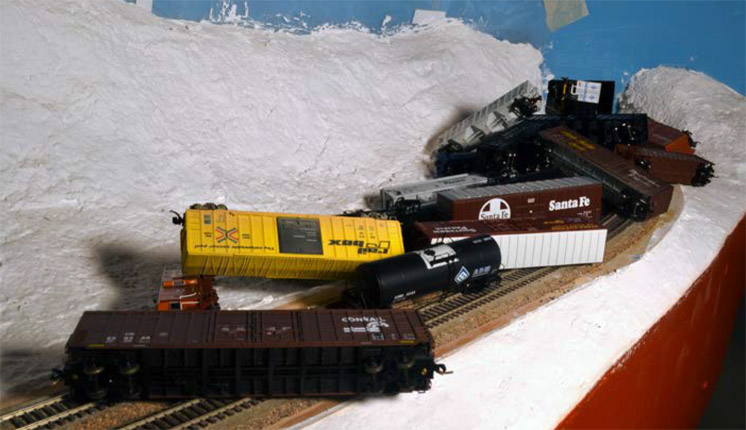
By way of illustration, let me describe the last accident I had on my N scale Tehachapi Pass layout’s helix, which thank goodness occurred a couple of years ago. The 20-car train was being pulled by two Athearn FP45s. About halfway up the 51⁄2-turn helix, the train separated behind the locomotive and started rolling back down, gathering speed quickly on the 2.5 percent grade.
I’ve had runaways on the open layout before, where I had a fighting chance of grabbing a car before the train has picked up too much speed. On the helix, though, there was a hardboard fascia between me and the train. All I could do was grit my teeth and pray. I expected to hear a rain of N scale cars hitting the concrete floor any second.
To my surprise, the cars stayed on the track all the way down, helped by the fact they were in a constant left turn. Once they roared through the portal in the backdrop, though, they’d be turning back to the right, and Newton’s laws and angular momentum being what they are, the train was doomed. I had some luck in controlling the pileup, but four cars left the railroad and hit the floor.
Three of them got off unscathed, but one was damaged beyond repair. Naturally it was one of my prized new Santa Fe covered hoppers from BLMA.
Don’t blame the helix. Those of you who’ve been reading these accounts of my adventures may recall my discussion of the helix and my initial problems with it. But those problems are now behind me. Trains now routinely glide up and down the helix without a hitch. Though the engineering issues are gone, a psychological problem remains.
The run in the helix is about 1.5 scale miles long, and takes about 4.5 minutes traveling at 20 scale mph. Engineers go mad wondering if the train is still moving, and when, if ever, it will reappear.
I have a solution in mind for that, a vertical slot in the fascia so the operators can see their trains as they pass.
The coupler was the culprit. I’ve learned that the Achilles heel of long N scale trains is usually the connection between the locomotive and the first car. The problem is that the couplers on the locomotives are body-mounted, while those on the cars are usually truck- mounted. When a heavy train hits a curve like in my helix, the side force pulls the car’s truck off the track.
At the time of this accident, I had a hard-and-fast rule: The car immediately behind the locomotive had to have body-mounts. Unfortunately, I hadn’t checked, and sure enough, the lead car on this train had truck-mounted couplers. The problem was compounded by the fact that the locomotive didn’t have Micro-Trains couplers. Since that time I’ve converted all the couplers on that train, and it’s since run dozens of times up the helix with nary a problem. Over the last few years, we’ve seen some new cars come with body-mounted couplers, and I hope this is the beginning of a trend.
I also believe you’re better off to equip all your locomotives and cars with the same brand of couplers. This is especially important for locomotives. My personal choice is Micro-Trains Magne-Matic couplers. Any of my locomotives that will be going up the hill and helix with long trains get converted to M-T couplers before they even attempt the journey.
When we tried running mid-train helpers, we quickly learned that truck- mounted couplers won’t get it done. Now they’re banned from my layout, but they sometimes manage to sneak back on.
Recently the video crew from MR Video Plus came to shoot the layout. (The video should be available on the MRVP site by the time you read this.) Model Railroader contributing editor Andy Sperandeo was backing a long train in the yard when a beautiful orange Illinois Central hopper derailed. He held the car up by one end like a dead fish. “Sure enough,” he said, “It’s got truck-mounted couplers.”
This column originally appeared in the September 2014 issue of Model Railroader – Ed.
After reading my “second edition” copy of Arthur Mellen Wellingtons book “ON THE PLACEMENT OF RAILROADS” multiple times I am glad I still intend to use switchbacks on my future N Scale mountain layout rather than a helix.
Having the opportunity to make more coniferous scenery, add 6 power for the climb whether is a through passenger or freight unit train with 50 plus cars and adding a pair of 6 axle helpers and caboose at the tail end of the consist to reach the tail track to quickly move the switches back to the rising grade as the climb continues and the conductors on the caboose and locomotive move the switches or shovel snow to clear it while the train is holding the grade with a compressor car on the helper locomotives and caboose.
One century later Mr. Wellingtons words still ring true no matter whos road it is. It is less expensive to build switchbacks than it is to dig tunnels under
mountains.
With todays modern construction methods and modern excavating machinery and better design methods using soil and rock core drilling, high strength concrete, tie back anchors, hurricane mesh to secure ground precast concrete blocks to secure soil walls, sheet piling to help anchor road beds in soft soils and soil and rock core drilling to determine what the soil and rock structure is along the desired route many problems can be solved before they even rear their ugly heads.
My reasoning is simple my arthritic hands make doing things more difficult.
Having a wide switch back allows for runaway tracks and good scenery placement on the grade with conifers on the wide shelf grade rising behind the track on the mountain with detailed sheet piling, concrete mafia block retaining walls, concrete snow sheds over the switches leading to the tail tracks and runaway tracks and as it climbs the grade to the next switch as the train continues upward to the next switch eventually reaching the rail yard to refuel and deliver coal for heating the town and service the passenger and MOW trains along with a locomotive shop and continue down the other side of the mountain.
It will be a lot of work and create a lot of realistic railroading when finished.
I had similar problems with truck mounted couplers connected to a body mounted coupler, especially with cars/engines with longer overhangs.
I have had issues where a particular combination of cars ran fine on all the curves on my layout, but kept derailing at one spot. The cause was a slightly misaligned rail joint. I had soldered it, but wasn’t careful enough and the following, truck mount truck flanges caught and derailed every time. This only happened with the longest overhang car (a Scale Trains auto rack. Beautiful car, by the way) followed by a car with truck mounts. It has the longest overhang of anything on my layout.
I think Jim needs to carefully look at the track in the helix. Maybe a slight misalignment at a rail joint where the flanges can catch, or a slightly tighter radius in that location. If the train runs fine on the same radius track but derails in one spot, then it’s the track.
Changing to all body mount couplers helps a lot, but can still occur if you have one long overhang car and one short one.
I hope this helps folks combat those pesky derailments.
I have a similar problem and am looking for a better fix. I have a 103.9 foot run of climbing/descending mainline under construction (HO). About half way up/down I have a 3.5 turn helix, Grade is 32 inches (2.57% average). As in the example, if a car or series of cars uncouple the result is the same when they come out of the helix and change direction. Much of my layout will be passing through numerous tunnels, usually short, but make it difficult to catch a runaway bunch of cars, short of setting up a blockade. What I am looking for are any ideas on how to control the speed of the runaway cars before they get to the extreme speeds the see if left unchecked.
Our HO club has a 4.5 turn helix. The track is 'Bullet Proof' – The operators are NOT! Climbing the helex usually is not an issue. Descending the helix needs a constant speed with no speed changes. We ask that operators make sure the jct switches at the bottom of the helix are aligned before starting down.the helix. Trying to stop a long/heavy train usually results in 'string-lining'. We use metal couplers and everything is body mounted. The plastic 'clone' couplers cannot withstand the stresses placed on them with a long train.
My club, The Whatcom Skagit MRRC N scale division, operates a helix inside a mountain with about 10 turns and is impossible to see the train. We solved this issue by purchasing an inexpensive color video camera (about $50 from Harbor Freight) and a member donated a older TV. We placed the TV in an easy to see location and now we can monitor the trains progress within the helix.
The TV is a hit during open house's as well.
One of the ideas about handling trains on a helix that I really like to "herniate" the helix about half way. The object in herniating the helix is to open the "bulgy" part so the engineer can see his train as it climbs or descends; giving him knowledge of where the train is at. It might also be possible (room permitting) to use this part as a passing track. That might improve operations. Probably less expensive than putting video cameras all over the place.
You might could also position the person with lowest seniority inside the helix as a monitor.
That's gonna make the news.
I wonder about the horror story's that you guy talk about with "N" scale. I do not have the problems like people say I should have with "N" scale. I back up at a slow restricted speed etc. who knows but do not have the same problems.