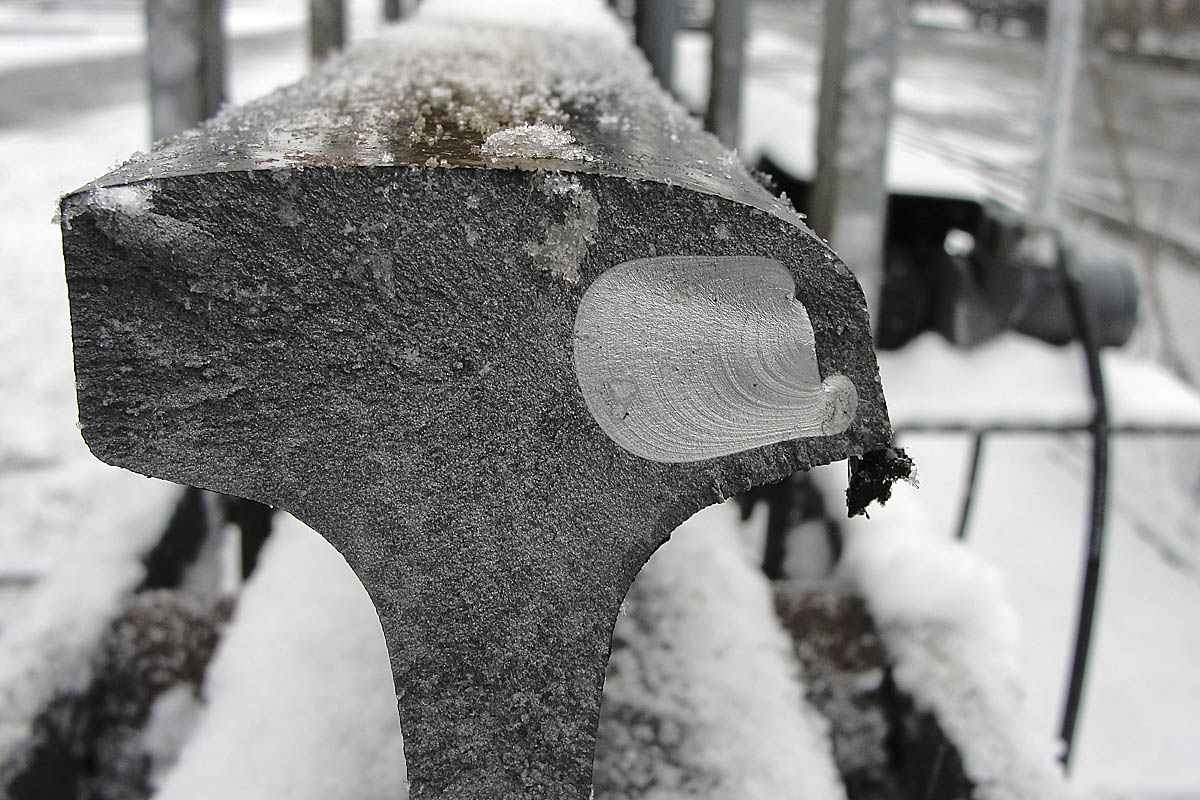
As railroads installed new rail in recent decades, the expectation was that it would not wear down as quickly as the softer rail that was installed in the 1960s and 1970s. While the expectation of slower wear has been met, the unexpected issue of minute cracks that can lead to breaks has required rail to be replaced well before the end of its service life.
“In the old days, the softer rails would deform to comply with the wheel loading that stressed the rail, but today, the much harder rail doesn’t handle stress in the same way,” says Gordon Bachinsky, president of Indialantic, Fla.-based Advanced Rail Management Corp.
The frequency of broken rail-caused derailments, both in absolute numbers and as a percentage of rail miles, has dropped in recent decades. Yet, the frequency of derailments due to other causes has dropped even more rapidly, leaving broken rails as today’s leading cause of mainline track derailments in North America.
Several factors are known to contribute to the problem of rail breaks, including occasional manufacturing defects and excessive cold temperatures that have dogged railroads for years. Railroaders are now paying more attention to the fact that loaded freight cars are also heavier than they used to be, with many weighing 286,000 pounds when loaded. Heavier loads have meant higher axle loadings that bear down on rails and these loadings are only expected to increase in the future. Recent rail route consolidations also have resulted in less track doing more work, particularly since the amount of freight moved by rail today is greater than ever.
Railroaders and researchers say the prime result of these increases has been a rise in the amount of small surface cracks formed by the forces of the wheel contacting the rail, known as rolling contact fatigue. By themselves, these small cracks do not usually pose a problem. Over time though, these cracks can grow and change their orientation, making a vertical turn that creates a “transverse defect,” which is a crack in the rail. If the defect is not detected and removed, it can grow and cause a rail break. Railroaders contacted for this article debated whether rolling contact fatigue is new to railroading but decided the problem is just more obvious now that rail cracks are no longer removed with daily wear from wheels.
This type of fatigue is common in metallurgy and appears as a form of “work hardening” in applications from roller and ball bearings to gears and flanged steel wheels, where the phenomenon can result in rare wheel shattering.
Railroads test track for a variety of defects, anywhere from daily on the Northeast Corridor to annually in other locations, often with help from specialized inspection companies. One of the challenges to detecting rolling contact fatigue is that early stage fatigue cracks are often less than 1 mm in length and avoid detection from magnetic field induction or sound wave-based ultrasonic testing equipment mounted in hi-rail vehicles or self-propelled cars. And that’s not all, according to Darwin Isdahl, vice president of asset management at Loram Maintenance of Way Inc.: “SSCs — shells, spalls, and corrugation — can interfere with the ability of ultrasonic equipment to see into the rail and can cloud the view of ultrasonic testing.” Although uncommon, wheel-slip burning of the rail from spinning locomotive wheels can also interfere with ultrasonic testing.
To counter these problems, railroads are exploring the use of eddy current inspection, one of several promising technologies under development. An eddy current is an electrical current that flows in small circles, like eddies in a stream, which is strongest at the surface and just below the surface of an object being inspected. Railroads hope that within a year or two, this technology will be able to measure the depth of these cracks, enabling track maintenance people to schedule a rail grinder to grind the cracks away.
The goal, of course, is to reduce the number of cracks before they get to the fast-growing stage, and to keep cracks under control while finding defects that are forming so they can be removed. Research shows that periodic grinding removes cracks and also seems to reduce rolling contact fatigue stresses within the rail.
Brad Kerchof, Norfolk Southern’s director of research and tests, says three key steps to reducing broken rails are: testing rails for flaws often enough that defects are found before they result in broken rails, ensuring the tests are of the highest quality, and replacing rail segments that show high numbers of rail flaws.