Storing locomotives
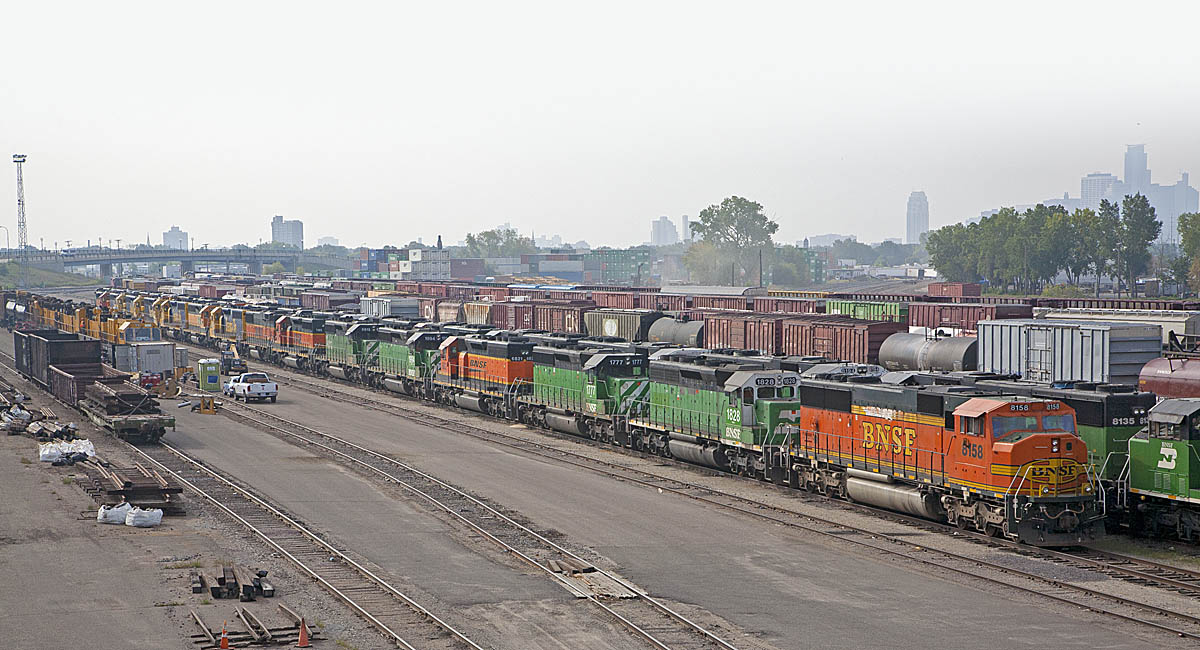
Changing traffic levels affect the amount of equipment in operation, from freight cars to locomotives. When events occur such as a softening of the economy, losing a major contract to haul goods, or the end of a cyclical demand such as a grain harvest, a railroad will occasionally have to store equipment when not needed.
When storing locomotives, a railroad will typically look at its fleet to determine which engines are the best candidates for storage. Different criteria are typically applied: the age of locomotives, performance and reliability data of certain models, and the current necessity of that particular locomotive type.
When a group is selected, the locomotives must be properly set up for storage. Generally the following must be done to a locomotive being prepared for storage.
No. 1: The most important step is draining the fluids that can freeze. The majority of locomotives use plain tap water with corrosion inhibitors added to the radiator system. This is done because water is a better heat transfer fluid than a glycol-based antifreeze solution.
No. 2: Placing a cover over the engine’s exhaust stack prevents rainwater or other objects from accumulating in the exhaust system of the engine.
No. 3: The locomotive’s batteries will be disconnected, though these may be removed and used elsewhere in a railroad’s fleet if the locomotive is going to be stored for an extended period of time.
No. 4: The locomotive’s cab will be prepped and secured, with the doors and windows locked to prevent vandalism.
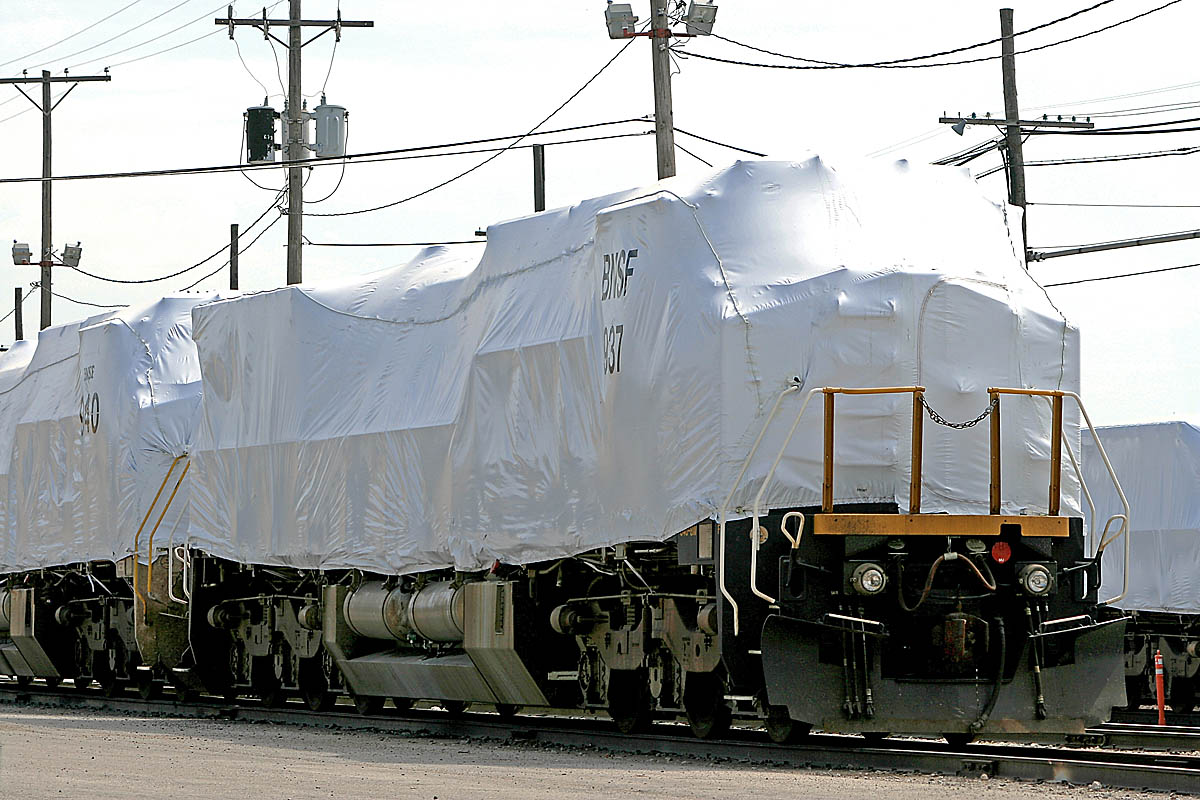
In a departure from the norm, BNSF implemented a pilot program in 2009 for select locomotives being stored that involved wrapping them in plastic shrink wrap from the frame up. Shrink wrap keeps all precipitation from entering the locomotive though various gaps between access doors, sheet metal panels, and grating. Unfortunately, the program was discontinued shortly thereafter due to the high level of condensation buildup in the cabs of the wrapped locomotives.
No. 5: Railroads must select a suitable storage location for locomotives to be parked for an extended period of time. Tracks may be available for storage at or near the same shop that’s prepping the units, making it convenient when the time comes to reactivate them. If the railroad doesn’t have storage close to the shop, mechanical forces must prep the units slightly differently to allow the locomotives to move dead in train to another location. When this happens, railroads tend to dispatch large groups of units for storage at once in a special move.
A storage location can affect the condition of the locomotive when it’s called for duty once again. Decades ago, long strings of stored locomotives could be seen in various areas of the desert southwest on many western railroads where the warm, dry days would keep the locomotives in better condition than a place that receives a large amount of moisture.
Locomotive leasing companies prefer to have their fleets in operation at all times, but there are periods when units need to be stored. When this occurs, they typically have to rent space to store locomotives on railroad property, third party contract shop grounds, or a private entity. Leasing companies try to select locations to store locomotives where they have easy access to their equipment and close to a shop that can perform work on stored locomotives when the next lessee for the units is identified. A leasing company may reposition locomotives for storage close to a locomotive’s next lease location if a deal is close at hand.
With coal and oil traffic off, let’s hope the lines of stored units are short and brief.
This story originally appeared in the January 2016 issue of Trains Magazine.
future preservation canadates might be lurking in those dead lines