I model the Western Maryland Ry. (WM) from the 1920s to before the start of World War II. Appropriate commercial models of coal hoppers for my modeling era are limited in large scale. I was using LGB two-bay and Bachmann three-bay hoppers as stand-ins, but I wanted accurate, period-specific coal hoppers for my rolling stock fleet.
I turned to 3-D printing to create models that aren’t available commercially. Over the last few months I created files, printed, and built different versions of the Vanderbilt, GLa, U-channel, and fish-belly hoppers that were operated by the WM and its predecessors during the era I model.
In this article series I’ll explain how I built the different WM freight cars [Read about Randy’s 3-D printed Vanderbilt hopper car and GLa hopper car on Trains.com — Ed.] If you have access to a 3-D printer, the files are available on Cults3D.
Among the early coal haulers used by Western Maryland were the two-bay U-channel hopper cars. The 50-ton cars replaced the railroad’s GLa-style cars, many of which were used for parts in the WM’s rebuild program. The hoppers featured Ajax hand brakes and an AB brake system. Early cars of this type had grab irons on the corners, but subsequent rebuilds had ladders. The U-channel hopper cars lasted well into the 1970s and wore both “fast freight” and “speed lettering” paint schemes.
When designing the 3-D printed model, I made the sides, slope sheets, and underframe each as two separate pieces to fit the limits of a standard 220 x 220 mm filament printer.
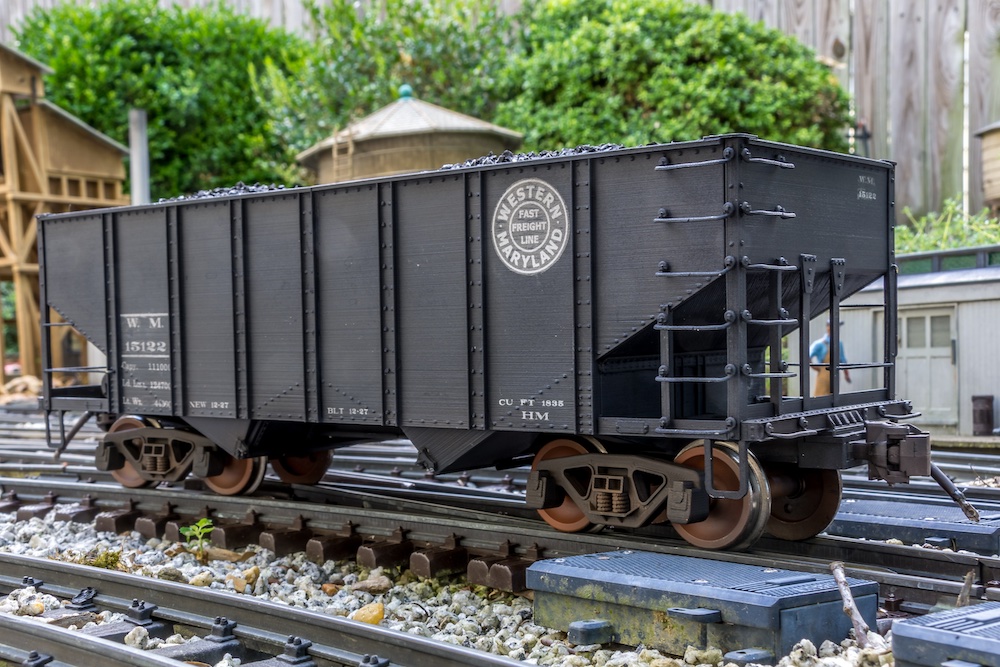
I used Tinkercad to create my files, and typically selected a scale of 1mm = 1” to make it easier to draw the files. This worked out to 1:25.4 scale, so I re-scaled my files in the slicer depending on what I was making. I built these cars in 1:29 scale, which worked out to a slicer rescale of 86%.

After printing the six basic hopper components, I did an initial test assembly to check the fit. I glued the two body panel sections together and used 1/8” styrene rod to join the two halves of the frame. Once the frame was set, I added the slope sheets to the frame assembly. I designed alignment pin holes in the frame and slope sheet pieces, which use a short piece of 1/8” styrene rod to ensure the slope sheets are properly aligned on the frame. After adding the frame/slope sheet assembly to the body panels, I glued everything together. Then I installed the frame/slope sheet braces to each end.
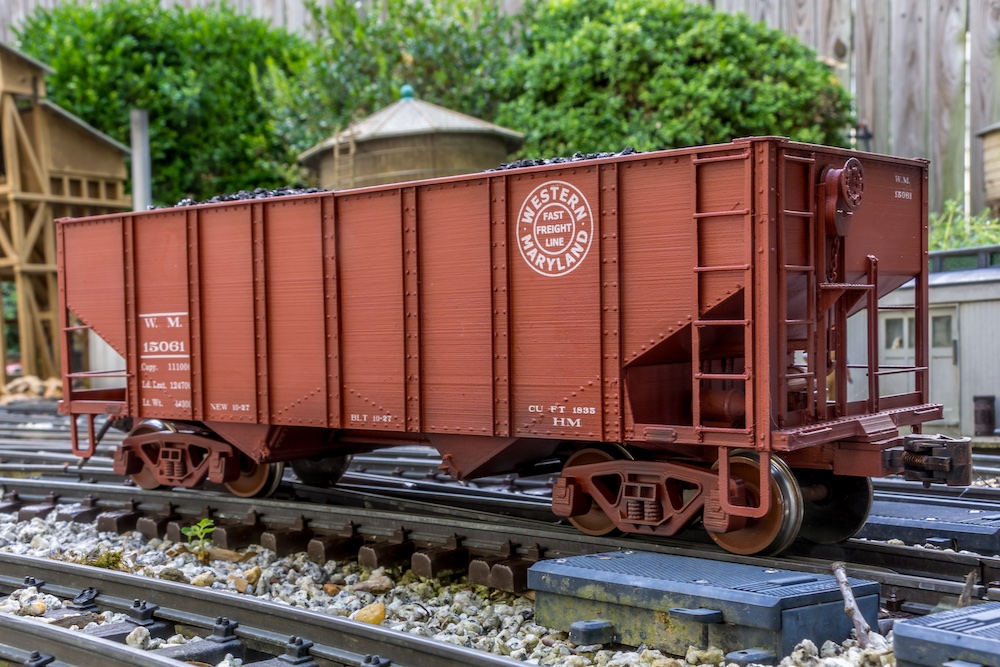
With the basic assembly completed, I started adding details like corner posts and interior braces. The first car I constructed depicted a rebuilt version with corner ladders. I installed the AB brake components and used brass rod for the lines between the air reservoir and control valve.
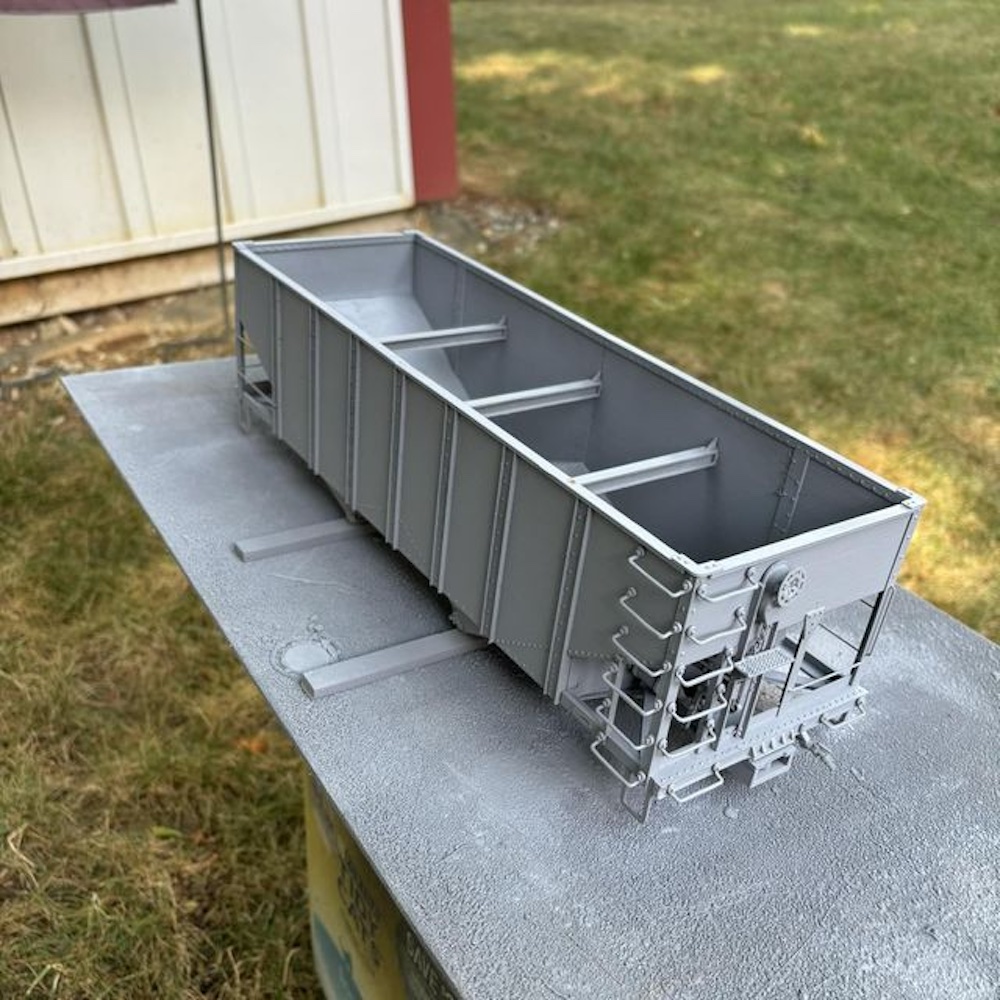
The brake platform has a mounting hole for a brass rod that runs from the hand brake chain to the fulcrum. I added grab irons to the end sills, as well as Ozark Miniatures train line hoses (1155), the latter installed into a separate 3-D printed mount under the edge of the sill. I installed Kadee center-set couplers into draft-gear boxes that I designed. The solid-bearing trucks were also 3-D printed. Metal wheels were the final addition before painting.
Once assembly was complete, I sprayed the hopper with gray primer. After that dried, I applied Badger Light Tuscan Red Oxide Paint (BAD-1614) with an airbrush. I used photos to re-create the fast freight lettering found on the prototype cars. I designed the decal artwork in Microsoft Publisher and exported a .PDF file, which I sent to Shawmut Car Shops for printing.
After I made the first car, I designed and printed another with the as-built grab irons on the corners. I painted this car in the earlier black paint scheme. I also made a 3-D printed load form for these cars, which I topped with aquarium charcoal to represent coal.
Wood-chip hoppers
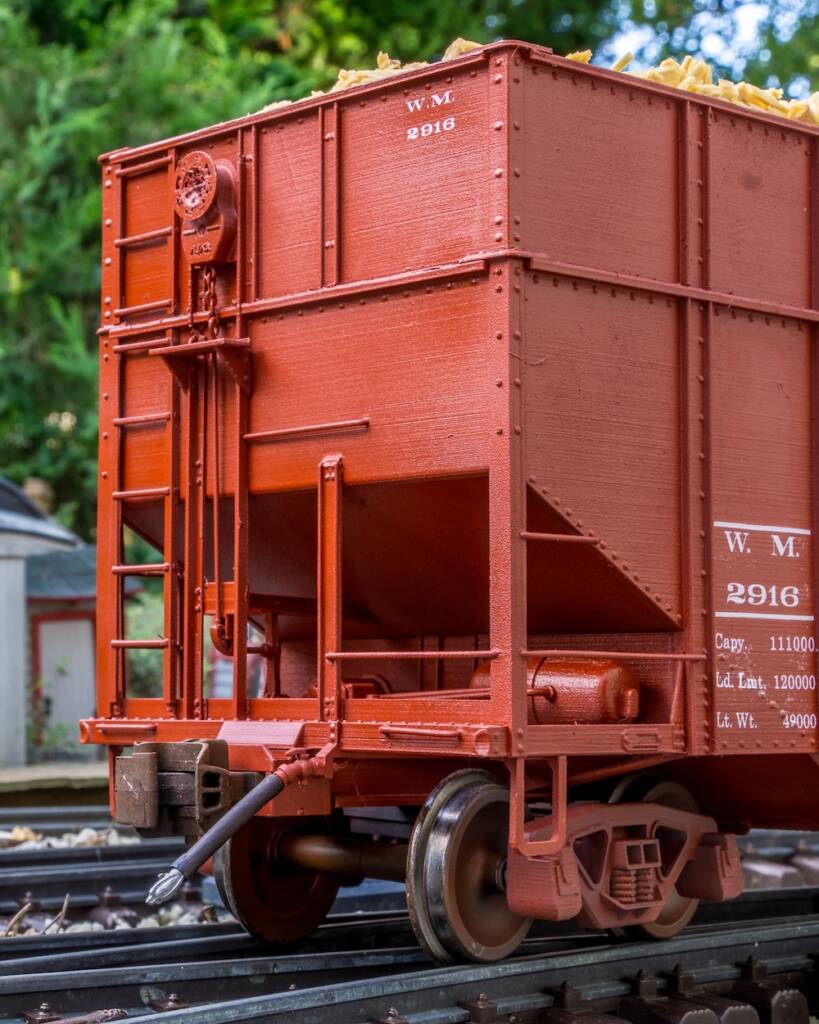
After building the two coal hoppers, I decided to make one of Western Maryland’s wood-chip hoppers as I already designed the file for the basic car. The WM converted a group of U-channel hoppers to wood-chip service in the 1960s by adding a three-foot extension on top to increase capacity.
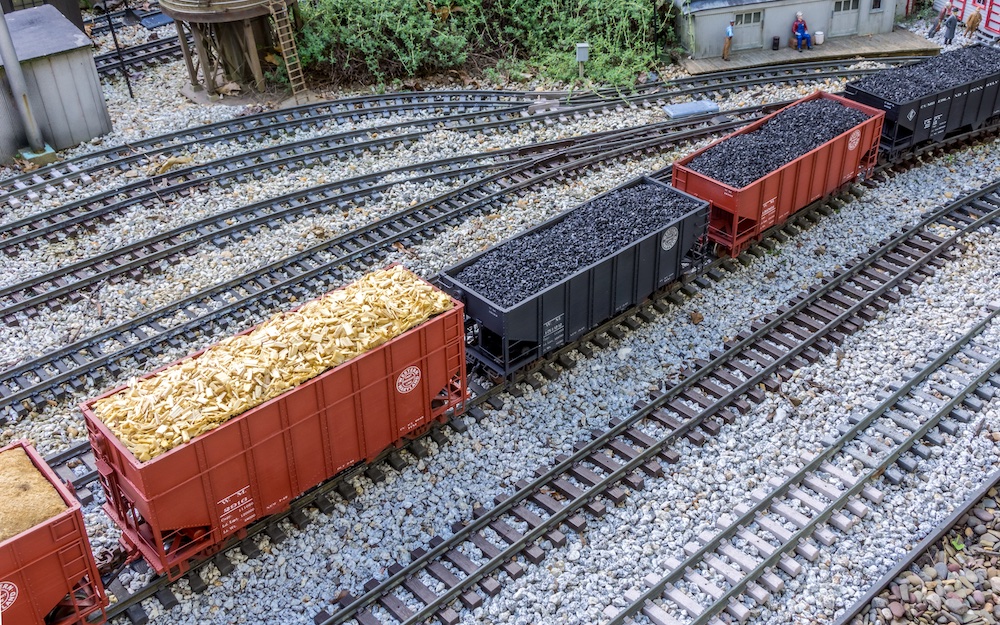
The extensions were made using the top sections of retired cars. The placement of the brake platform and brake wheel were modified to be higher on the car, but the rest of the car was essentially the same. I made my 3-D printed version in a similar fashion, cutting and pasting the top of the carbody files to make the extensions. I modified the brake placement and brake platform assembly to match the prototype. After priming the car, I airbrushed it with Badger Light Tuscan Red Oxide.
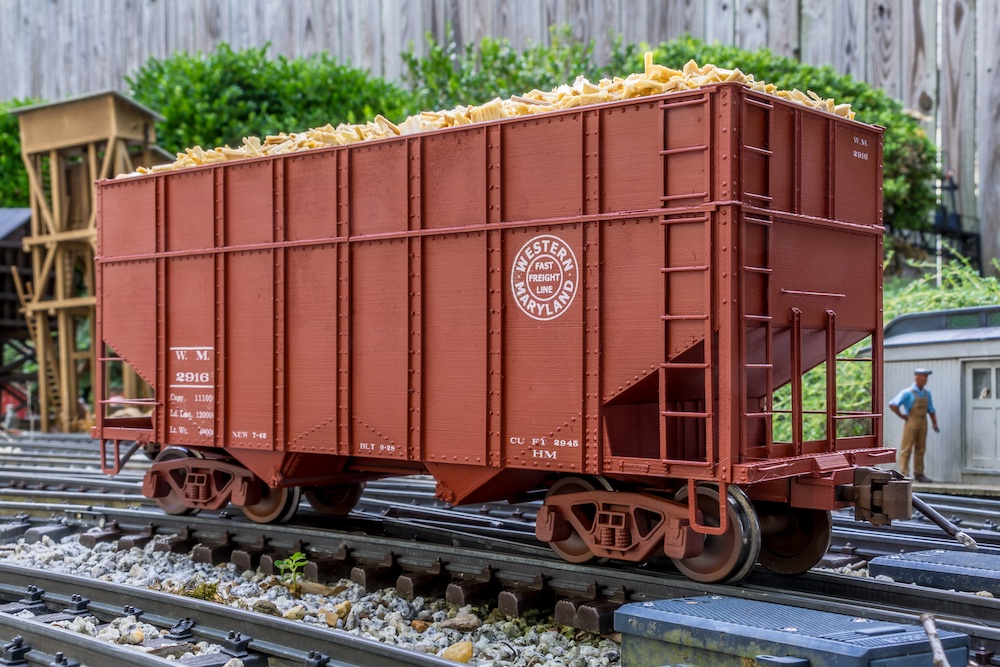
The full-size cars wore the speed lettering scheme when they were rebuilt, which is outside of my modeling era. Using some modeler’s license, I applied the fast freight herald to the sides so it would fit with my other equipment. One of my garden railroad friends made a wood-chip load for the car using small pieces of wood he cut up and chopped with a kitchen blender. He glued those pieces onto a base that rests on top of the hopper.