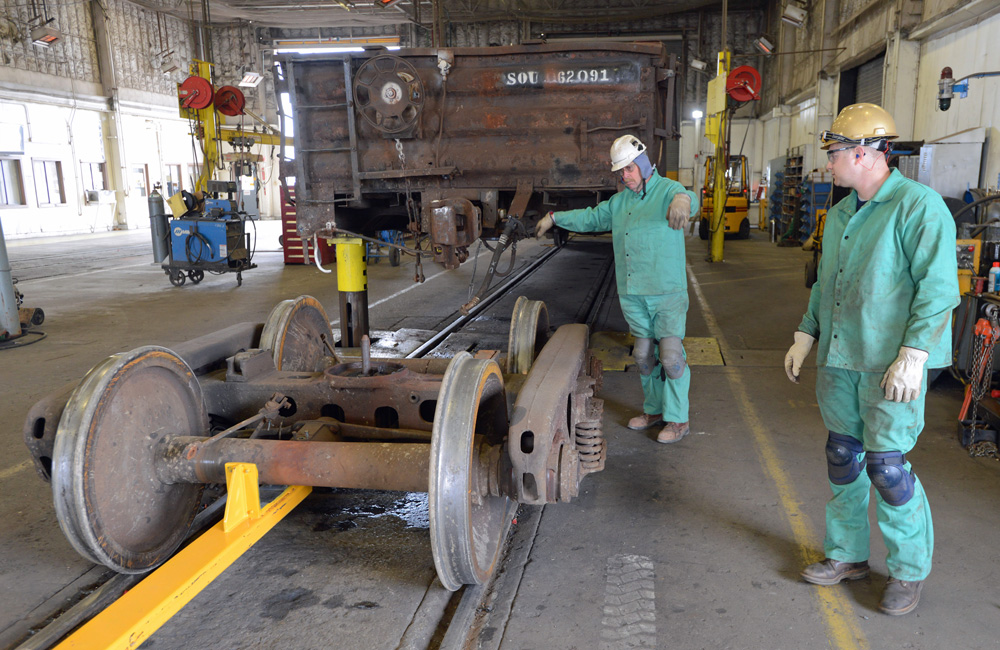
Q: Reading Jerry Dziedzic’s essay on “Turning waybills into dollar bills” (August 2023) made me realize that I don’t know anything about how prototype railroads handle the inspection and shopping of freight cars. Are cars sent in for inspection, paint, and maintenance at fixed times, or after a certain number of miles, or only when a problem is found? And how are these car moves handled operationally? It seems like this could be a logical source of traffic across my pike, or even a new “industry” if I found space to model a car maintenance shop. – Mark Herrman
A: Railroads were pretty serious about inspecting and maintaining their rolling stock. The Interstate Commerce Commission (and, after 1966, the Federal Railroad Administration) requires regular inspection and maintenance of railcars, which is meticulously documented both in the railroad’s records and on the cars themselves. Car markings such as a REBLT date and, more recently, the Consolidated Stencil (mandated by the Association of American Railroads) list when cars’ brake equipment, bearings, and more were last inspected. The federal regulations on railcar inspection are enumerated in the Code of Federal Regulations, Title 49, Subtitle B, Chapter II, part 215, which is available online if you really want that kind of detail.
To summarize (or, as the kids say these days, “tl;dr”), regular in-depth inspections are scheduled after a certain amount of time or miles have gone by. In addition, a car must be inspected for defects every time it leaves a station. This can be done before or after it’s placed in a train. Among the items that must be inspected are the wheels, axles, bearings, trucks, underframe, draft gear, couplers, and safety equipment. Trains are also usually subject to an informal “rolling inspection” whenever they pass a railroad official in a yard, station, or tower. This isn’t an in-depth examination, but more of a cursory look to spot obvious defects like dragging equipment, broken doors, leaking lading, or hot journal boxes. On top of all that, railroads have automatic trackside equipment to identify and notify officials of dragging equipment, derailed wheels, and hotboxes. Bad equipment is bad for the bottom line, so the railroads generally don’t mind subjecting their rolling stock to this frequent scrutiny.
In the case that such a defect is found by any of these means, the car is “bad ordered.” The car is usually set out immediately, and a visible card or sticker (the “bad order” tag) is applied to the car, usually on the door if it’s a boxcar or the like. This tag includes information like the reporting mark and car number, the name of the inspecting railroad, the nature of the defect(s), and where the car is to be taken for repair. If the car is loaded, it’s generally not unloaded unless it is necessary to do so to affect the repairs and the unloading point is along the route to the repair site. The car is then moved to its home road for repairs. The bad order car is generally moved in a special movement, not a regular train, because many types of defects call for restricted speeds.
Depending on how extensive the needed repairs are, the car might go to a RIP track (“Repair In Place”) or a car shop. Often found in or near classification yards, RIP tracks can handle quick repairs like repairing a broken grab iron or door latch, repacking a wheel bearing, or swapping out a broken coupler. More extensive work involving a car’s trucks, structural members, or brake gear must be done at a car shop. Most railroads have at least one of these, usually situated at a major yard or engine terminal, but smaller roads might contract their major repair work to an outside company or another railroad.
How might you use this information to add maintenance operation to a layout? First, you’ll need somewhere to take your bad order cars. Even if you don’t have space for a car shop, most model railroads can fit in a RIP track. Designate a yard spur to receive bad orders and situate details alongside it like a tool shed, welding equipment, worker figures, replacement wheelsets, and piles of broken junk. A larger repair facility might also have items like a repair shed, a paint shop, or an overhead crane.
Now for the fun part. Get a stack of index cards and, if you route cars with car cards and waybills, cut the index cards to fit the pockets on the car cards. On 95% of the cards, write “Good inspection – no defects.” On the remaining 5%, write “Bad Order” and the name of a random car defect like “Missing grab iron,” “Flat wheel,” “Bad wheel bearing,” “Damaged door,” or “Broken coupler.” Add on which car in the train the defect is in (“Second boxcar,” “Third car after engine,” “Last car in train”) and, if appropriate, a speed restriction. Then shuffle the bad orders in with the other cards, and whenever an engineer picks up his train, have him draw an inspection card. A bad order card means he must set out the bad car on the RIP track, if there is one in the yard, or on a spur to be moved by a maintenance-of-way train if not.
If you have a car shop on your layout, you can also add to the rotation of car movements an occasional special movement to the shop for regular inspection. Adding events like this to your railroad can bring variety to your operations and keep your engineers on their toes.
Send us your questions
Have a question about modeling, operation, or prototype railroads? Send it to us at AskTrains@Trains.com. Be sure to put “Ask MR” in the subject.