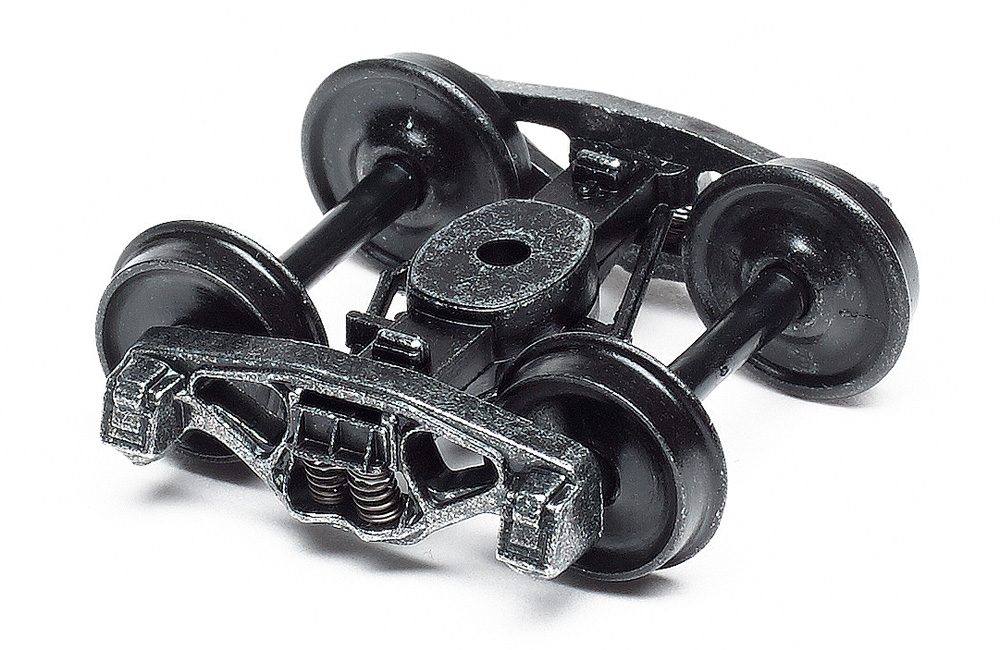
Q: I want to replace some wheelsets on my 1:32 passenger cars but don’t know where to measure the model railroad car wheels’ diameter. I’d like to keep the wheel sizes the same with the new as the old so I don’t need to deal with altering the height of my couplers. Is the wheel diameter measured next to the flange or out on the edge? – Bruce Jahn, Livermore, Calif.
A: According to the National Model Railroad Association’s Recommended Practice (RP) 25, Wheel Contour, the diameter of a model wheelset is measured at the widest part of the tread, next to the flange. (You can download the NMRA’s data sheet on the RP-25 wheel contour from the NMRA’s website.)
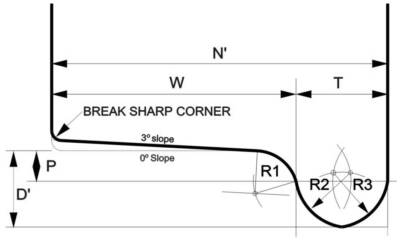
As you can see in the diagram at right, the tread of a railroad wheel – be it on a model or the prototype – is not cylindrical, but is a section of a cone. The tread slopes at an angle of 3 degrees, making the diameter of the wheel tread closest to the flange wider than the diameter at the inner edge. There’s a reason for that, and it’s not just because it makes wheels easier to cast in one piece. It’s because rail wheels are fixed to solid axles. This keeps them a fixed distance apart and parallel to each other so they don’t wobble off the rails.
However, it also prevents them from turning at different speeds to handle curves. Since the rails on the outside of a curve are longer than the ones on the inside, wheels that couldn’t turn at different speeds would slip. But since the wheels have a conical profile, as the rails in a curve start to bend, the outside rail turns toward the flange, where the diameter is larger. Meanwhile, the inside rail bends away from the flange, where the diameter is smaller. Therefore, even though both wheels make the same number of revolutions, the inside wheel travels a shorter distance than the outside. Although you can still hear the squeal of slipping wheels on tight curves, most curves on the prototype are gentle enough that the slight difference in diameter between the inside and outside of the wheels compensates for that.
Curves on model railroads are generally much tighter than those on the prototype, but the wheel-slippage issue still doesn’t really matter to us, since model cars are light enough that wheels can slip as needed without causing excessive noise or wheel and rail wear. Model wheels still have that slight difference in inner and outer diameters, though, both because they’re easier to mold and because it’s more realistic.
Although the NMRA has the RP-25 specification governing the shape of a wheel, there isn’t a standard for the diameter of a wheel, because on the prototype, wheels come in all kinds of different sizes. Today, most railcar wheels come in one of four different sizes: 28”, 33”, 36”, and 38”. Although there are exceptions, the rule of thumb is that 100- and 110-ton capacity freight cars ride on 36” wheels; passenger cars also use 36” wheels; auto racks and low-profile 70-ton piggyback cars have 28” wheels; and 70-ton cars, which includes most older cars, roll on 33” wheels. Some intermodal cars fitted with 125-ton trucks have 38” wheels.
As you mentioned, it’s important to make sure that you replace your cars’ wheelsets with wheels of the same size. So don’t go by the rule of thumb, but rather measure the model railroad car wheels before buying replacements. But since the slope of the wheel tread is just 3 degrees, even in large scale, the difference in diameter between the inside and outside of the tread will be negligible. A scale rule should be accurate enough to tell you what size wheels you’re dealing with.
Send us your questions
Have a question about modeling, operation, or prototype railroads? Send it to us at AskTrains@Trains.com. Be sure to put “Ask MR” in the subject.