While on a recent trip to the National Model Railroad Association’s Southeast Regional Convention in Decatur, Ala., I was fortunate enough to go on a trip to Huntsville’s International Intermodal Center. Right when our van arrived in the parking lot, I knew that this would be a perfect real-world industry that anyone can model on their layout.
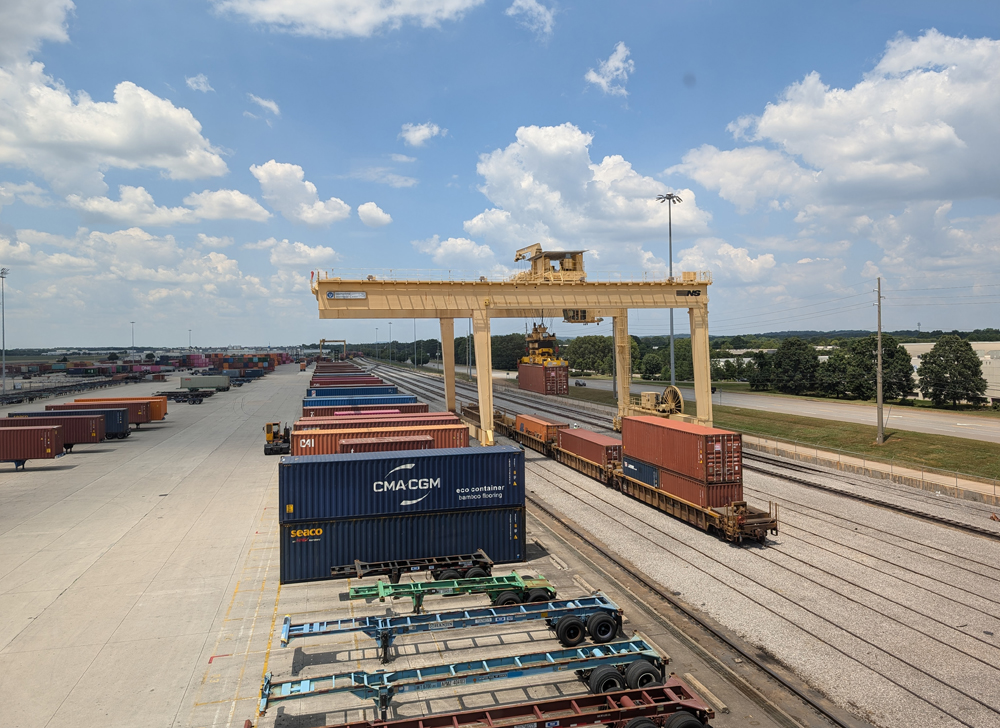
International Intermodal Center
Huntsville’s International Intermodal Center is operated by a small team within the Port of Huntsville’s Global Logistics Park, which also connects to the Huntsville Airport. The center has a direct partnership with Norfolk Southern. A five-mile long spur connects the center, along with various other industries along the spur, to Norfolk Southern’s mainline through Huntsville.
At its largest point, the center has four loading/unloading tracks with two 45-ton overhead cranes doing the work. Intermodal cars are switched using two locomotives: No. 8652, an Electro-Motive Division (EMD) SW900, and No. 2383, an ex-Norfolk Southern MP15E. Previously an RS3 was also on the roster.
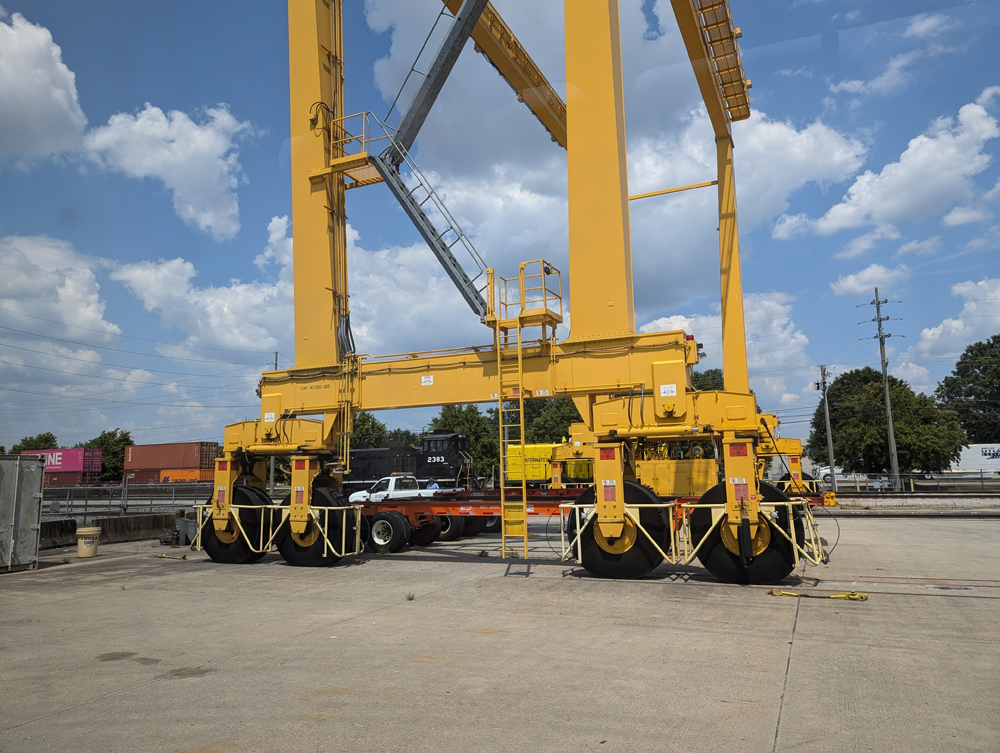
The port receives, transfers, stores, and distributes all container sizes from 20-foot to 48-foot for customers throughout the United States. Containers can be stacked by a Kalmar crane for storage, and placed on chassis when they’re ready to be shipped. While it’s not the largest intermodal port by any means, the center had 27,597 lifts in 2023, which was 24 percent more than in 2022.
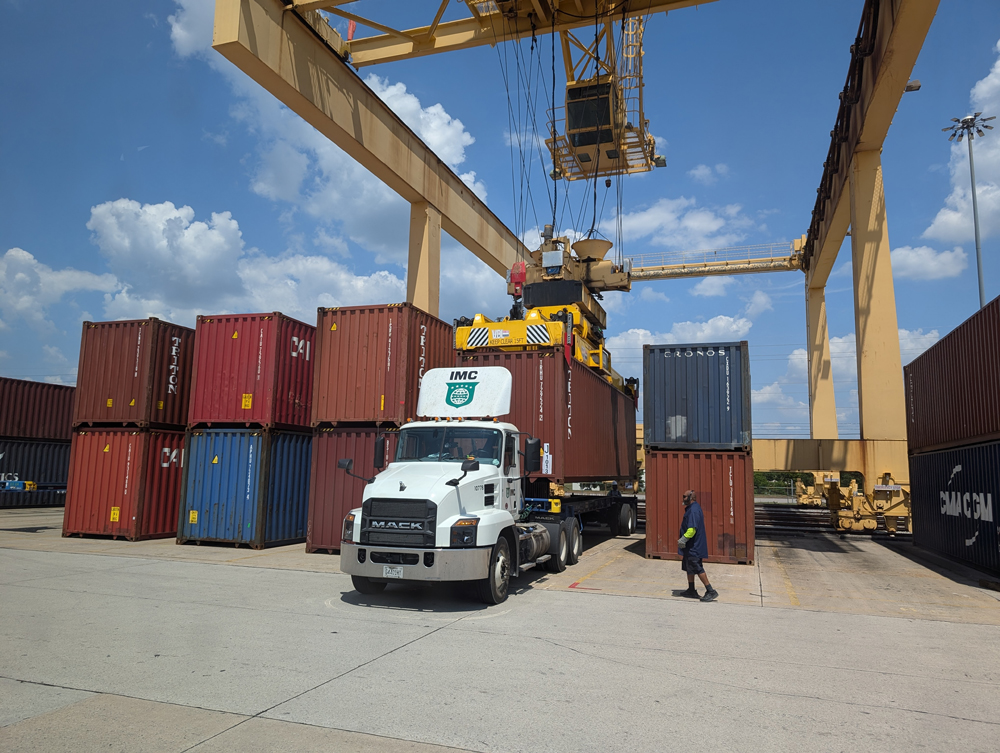
Modeling the facility
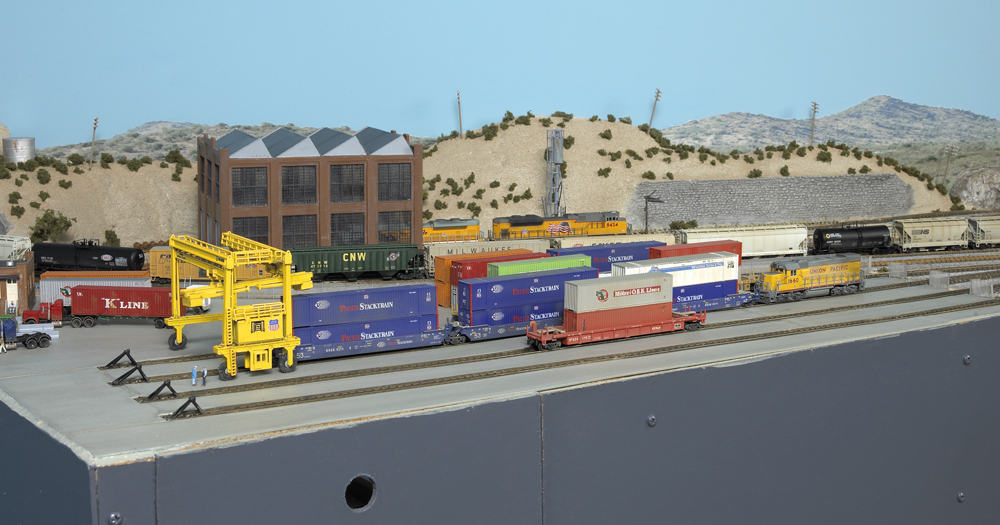
My first thought when seeing the facility was that it looked really similar to the intermodal yard on the N scale Salt Lake Route project layout from 2010. The yard had four stub-end tracks, just like the Huntsville facility, and one overhead crane. On the Salt Lake Route, Dick Christianson used Kato Unitrack, cork, and sheet styrene to create the level-pavement of an intermodal yard. Now, 14 years later, it’s easier than ever to do this by purchasing Kato’s Unitram Freight Depot set. This modular product takes two tracks in a double-track configuration and squeezes them together before connecting to the pavement. Extensions are also available to create a longer terminal. Sections can be connected together to create a yard with as many tracks as you want.
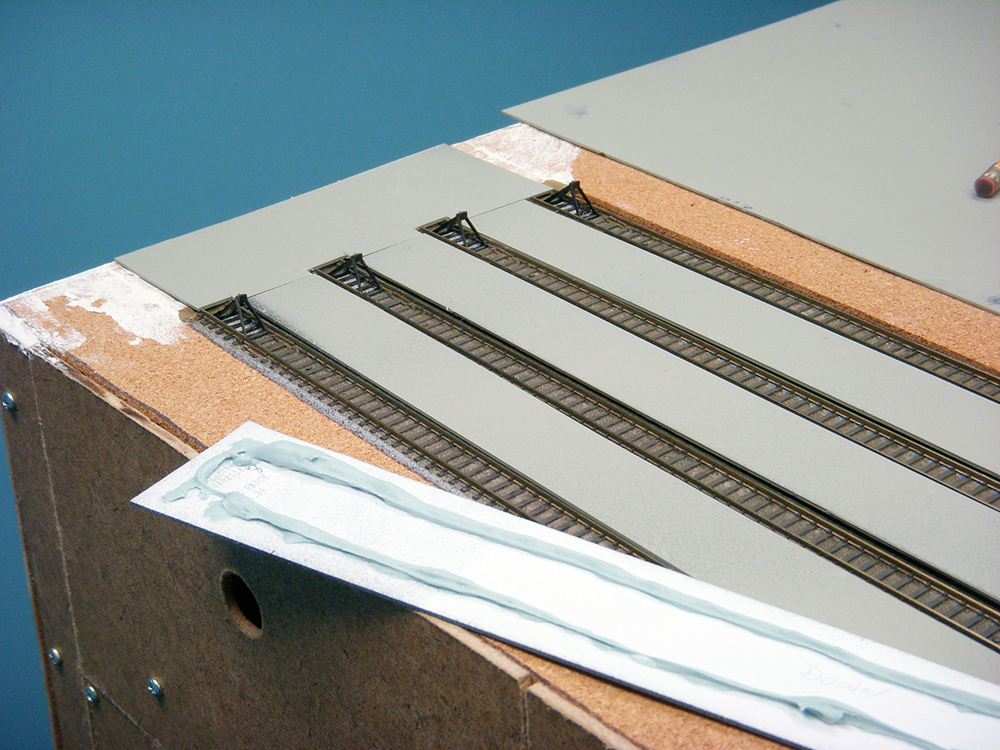
If you’re not using N scale Unitrack, install a cork sheet that’s the same height as the ties on your track. Then cut pieces of .030” styrene to create a concrete surface level with the height of the rail. This technique will also work in HO scale, though you may need to adjust the thickness of the cork and styrene.
Another way to create the yard in HO scale is by using the Walthers intermodal yard pavement kit. Much like Kato’s product, this kit is modular, allowing for expansion. It features multiple paving sections including landing pads, roadway, craneway, concrete grade crossing, crossing center, and crossing edges. All of those parts are molded in concrete gray with surface texture.
In addition, Walthers offers a set of intermodal yard details containing ATV/UTV crossings and non-operating solar-powered switch machines. Both modular options, as well as the homemade option, allow you to make the intermodal yard as long as the available space permits. The Huntsville facility is proof that an intermodal terminal doesn’t need to be several miles long.
Senior Editor Cody Grivno also pointed me to Model Railroad Planning 2000 which contained an article on the Huntsville intermodal facility, starting on page 50.
Modeling cranes
Now is my personal favorite part, the cranes. Walthers produces Mi-Jack cranes in both N scale and HO scale. These non-operating cranes are fun to build and add to any layout. They even include magnets that allow the crane, in a raised position, to hold magnetic-compatible intermodal containers.
If you want to go all out, find yourself a Heljan HO scale operating intermodal crane. While hard-to-find, this crane includes the pavement baseplate and space for five parallel tracks, with an optional extension sold separately. The crane can pick up, rotate, and transfer containers to/from intermodal cars and trucks. It even includes light-emitting diode lights for around-the-clock operation.
For smaller vertical operations, such as creating stacks of stored containers, Walthers also produces a Kalmar crane. The crane won’t load or unload containers off of railcars, but it will load and unload trucks. However if you want to load or unload trailers or containers from railcars, Wheels of Time has produced the PC-90 Piggy-Packer in both N scale and HO scale.
Other structures that you may consider adding are a yard office and entry/exit gate. And to secure the facility, a chain link fence should be installed around the yard. Lights are a smart addition for nighttime operations, and you’ll obviously need trucks, containers, and chassis. Manufacturers such as Walthers, Athearn, Herpa, and Jacksonville Terminal carry a wide variety of intermodal equipment.
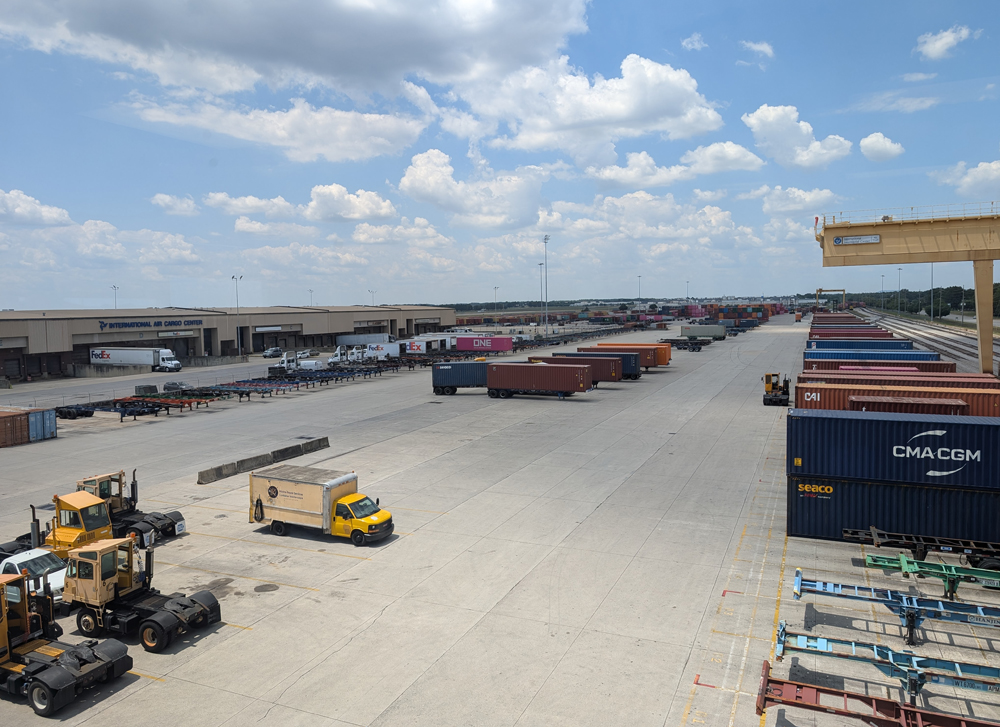
Operations
Unlike industries that receive a few cars from a local, intermodal terminals typically receive large cuts of cars or entire unit trains. The Huntsville facility receives cuts from NS. These cars are typically either all loads or all empties. The cuts are dropped on the facility’s receiving track, and then one of the switchers moves the cars into position for loading or unloading by the crane.
Since Huntsville is a shorter facility, only a small cut of cars can be loaded or unloaded at a time. We never saw more than a five-car set being loaded or unloaded at any given time. This creates a lot of short switching movements by operators. And then when the cars are loaded or unloaded, they go back to the interchange track for the next NS train to pick up.
Growing up near where CSX was building its Northwest Ohio Intermodal Terminal, intermodal facilities have always piqued my interest. Early on I realized that there was no way I could ever model a facility that big and have room for any more layout. After visiting the Huntsville terminal, it’s clear that there’s precedent for smaller stub-end terminals and they’re something that any modern modeler can build.