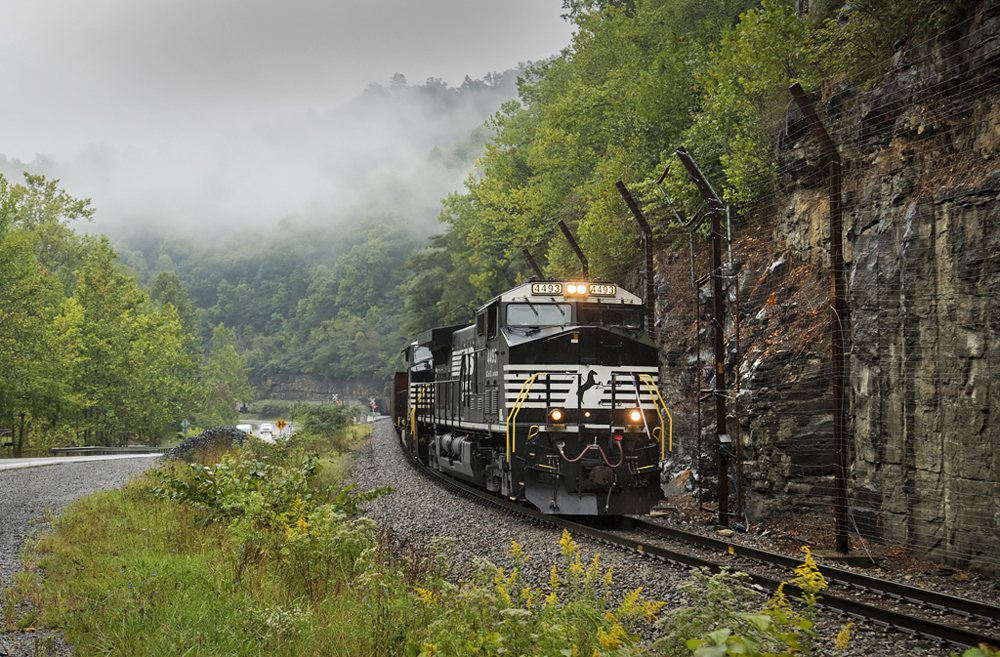
Part two of a look at the U.S. coal industry.
CHARLESTON, W.Va. — The COVID-19 pandemic may have shuttered economies and slowed industrial momentum, but a global rebound is helping coal producers refocus their long game on metallurgical coal investment as a broader initiative to diversify the sector. Met coal is a higher-priced coal used in the steelmaking process.
Railroads have longstanding relationships with producers in both industries, so as coal mines turn their focus to met coal, it’s natural that railroads will benefit in linking mines with the mills. Demand for metallurgical coal is driven by demand for steelmaking, and while steel demand fluctuates, as illustrated by the pandemic, it represents a reliable customer base for coal producers, compared to focusing only on electric utilities and the coal-fired power plant business.
For example, Arch Coal announced in early September it had begun operations at its new Leer South longwall mine in Barbour, W.Va. The loadout is located on the Appalachian & Ohio’s 158-mile railroad connecting with CSX Transportation’s ex-Baltimore & Ohio Mountain Subdivision at Grafton, W.Va.
Arch Coal’s $400 million investment in Leer South is expected to reach full production by the start of 2022. To quantify those tons as railcar loadings, if Leer South achieves its annual target of 4 million tons, that’s equal to more than 36,350 carloads per year — or around 300 trains per year, based on a 110-car unit train. Even at 2 million tons by rail, it remains a considerable volume that benefits the short line and Class I railroad.
Similarly, CONSOL Energy has resumed construction at its Itmann mine in southern West Virginia after pandemic-related setbacks. CONSOL is investing $90 million to develop the Itmann site, which will be capable of producing 900,000 tons of its own metallurgical coal and up to 1 million additional tons of third-party coal. A recent article by the Pittsburgh Business Times notes CONSOL is targeting a start date of late 2022. When complete, CONSOL expects a rate of return of around 25% spanning a 20-year period.
Itmann is located about 5 miles west of Norfolk Southern’s Elmore Yard near Mullens, W.Va., on the railroad’s ex-Virginian Railway Guyandot River Branch. Once completed, CONSOL’s newest West Virginia investment will have direct access to NS’s network, including access to NS-served domestic steel mills and the railroad’s Lamberts Point Coal Terminal in Norfolk, Va.
As coal producers share updates on their metallurgical projects, the U.S. steel industry is touting its growth in response to a recovering economy. According to the American Iron and Steel Institute, U.S. steel mills shipped 8.27 million tons in July 2021, a 37% increase from July 2020. This year, steel shipments are up nearly 15% compared to 2020 volumes.
Demand is particularly strong with corrosion-resistant sheet steel and strip, up 23%; cold rolled sheet, up 17%; and hot rolled sheet, up 9%, the institute notes in a year-over-year comparison through the end of July 2021.
U.S. coal feeds a global appetite, too
As coal producers market to steelmakers around the world, having access to rail-served export facilities will remain integral. Coal-exporting facilities across the U.S. handled 10.3 million tons of metallurgical coal during the first three months of 2021, while much of the nation was still waiting a vaccine rollout. Of those 10.3 million tons, more than 6 million tons, or 58%, was exported via Norfolk, Va., where NS and CSX operate coal export facilities. Mobile, Ala., is the second large player, having handled 2.2 million tons, or 22% of the country’s coal exports in those first three months. In Mobile, exporters like Warrior Met Coal gain access to international customers via the Gulf of Mexico. The third largest export facility is Baltimore, Md.; it handled 1.7 million tons, or more than 16% of the export market. Both CSX and NS serve the Maryland port.
Countries with the biggest appetite for coal are led by China, which consumed 2.3 million tons of U.S. met coal in 2021’s first quarter. Brazil is the second largest consumer, having received nearly 1.6 million tons during the same period. The Netherlands, in third, handled more than 905,000 tons. Japan, India, and the Ukraine also handled more than a half a million tons during the same period.
It’s no surprise that these exported volumes correlate with an analysis from the National Bureau of Statistics of China that Chinese steel mills produced nearly 12% more steel in the first half of 2021 compared to the same period in 2020. China also achieved a record-breaking month in May when it produced 99.4 million tons of steel, according to a Reuters report.
Likewise, Brazilian steelmakers are experiencing their highest monthly production rates since October 2018. In May, the country produced more than 3 million tons, equal to a 40% growth compared to May 2020.
As coal producers and the tightly linked rail industry focus on the coal marketplace post-pandemic, it’s a sure bet that investment in the sector will be on met coal.
Previously: “Analysis: Thermal coal demand trends upward as natural gas prices rise,” Sept. 23, 2021
Mr Ray
To clarify, met coal is used to make coke, iron ore (pellets) limestone and coke are fed into a blast furnace where the coke becomes the fuel to make liquid iron. The iron is then put into a basic oxygen furnace along with scrap and oxygen is used to melt and mix the two making steel. process was developed in the late 40’s and started being widely used in the 50’s and 60’s eliminating the open hearth process.
The latest (now 40 years old) and most efficient using no coal, maybe a small amount of coke for carbon content is the electric arc furnace (EAF), using only scrap steel.
Cliffs has developed an iron ore pellet that can be added to the EAF process to increase the quality of this steel from this process.
Several integrated mills are moving in this direction and this will cut into met coal but not in the short term.
This is a result of sound research and is part of the world trying to rid itself of coal, there is a seven year project at a large North American steel mill to make this conversion.
Thanks for that. And aren’t Swedish smelters moving to hydrogen furnaces? I can’t imagine they wouldn’t want to export that technology.
Either way, I can’t blame coal producers for focusing on metallurgical coal, but any Class I railroads hoping to profit from that are almost certainly going to be disappointed.
Simon, I forgot about that new process, it seems to be gaining ground.
Hydrogen is used in the blast furnace instead of coke to produce the molten iron before going to the BOF.
This will definitely reduce the amount of met coal used in the steel making process.
Met coal is used in blast furnaces for steel production from iron ore but the industry is migrating toward basic oxygen furnaces, using scrap, which are less energy intensive and ‘greener.’ In addition half of the world’s iron supply goes to China where a substantial portion is used in its construction industry. With the ongoing collapse of Evergrande and contraction in the rest of China’s residential construction plus China’s forthcoming population reduction the future for Chinese iron (and met coal) consumption is cloudy. In the immediate future China has slowed steel production as it wants clean skies for the 2022 Winter Olympics plus its (Xi Jinping’s) insane goal of reducing current energy consumption by 3 % (and you thought Europe’s politicians were crazy); many factories in China have shut down to cut electricity consumption. So the immediate future for met coal is murky.