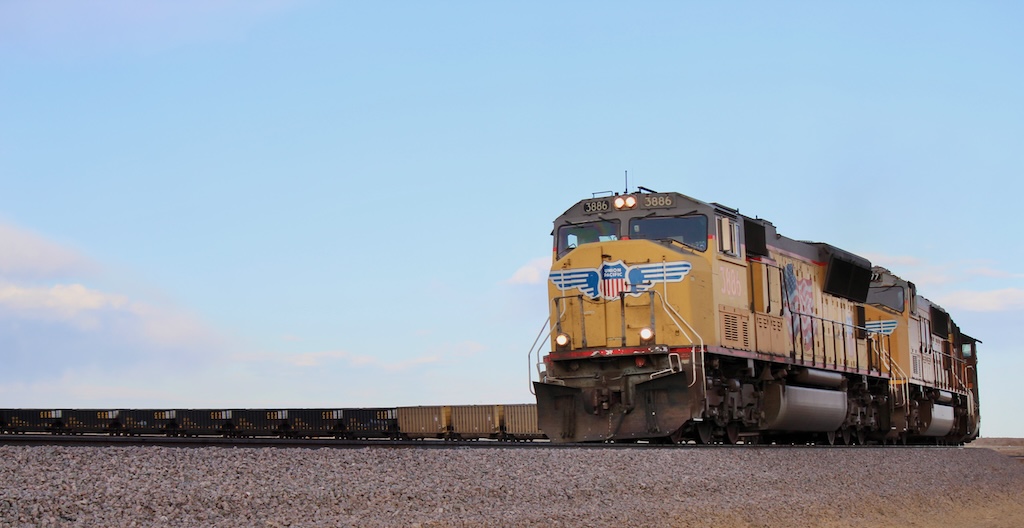
PUEBLO, Colo. — For a guy who goes around in circles at work every day, MxV Rail locomotive engineer Mike Walfoort sure gets a lot done. At the beginning of each 10-hour shift he climbs aboard an SD70M that’s on the point of a 114-car train of surplus coal gondolas. He slowly notches the throttle out to get the train’s 18,000 tons up to 40 mph. And then, if all goes well, by the end of his shift Walfoort will have made 120 to 130 laps around MxV Rail’s new Facility for Accelerated Service Testing.
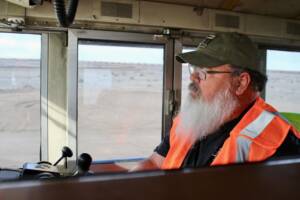
Walfoort’s 4-minute, 11-second trips around the 2.8-mile FAST loop track in Pueblo, Colo., add up in a hurry. Over the course of a year, the train will roll off nearly 25,000 miles and put an astounding 140 million gross tons on FAST’s single track. That’s more tonnage than the CSX or Norfolk Southern multi-track main lines carry in and out of Chicago every year.
Concentrating so much tonnage on so little mileage is what makes the $10 million FAST track the railroad industry’s proving ground. “We’re hitting it with a bigger hammer than revenue service does,” FAST Program Manager Chris Johnson says of the loop.
Data gleaned from 31 test sites scattered around FAST allow the MxV Rail research team to better understand the punishment that the one-two punch of high tonnage and heavy axle loads inflict on track. And their research in a controlled environment that mimics revenue service helps suppliers and railroads design, test, and develop track and equipment that is safer, lasts longer, and requires less maintenance.
“This could be the most impactful 2.8 miles of track in the industry in terms of advancing the science of railroading,” says MxV Rail CEO Kari Gonzales.
Moving Forward
FAST operations began in 1976. The previous FAST track accumulated more than 5 billion gross tons in its nearly four decades of operation. That loop was located at the Transportation Technology Center in Pueblo, a Federal Railroad Administration facility that the Association of American Railroads took over amid federal budget cuts in 1982.
The FRA and AAR subsidiary TTCI went their separate ways in 2022, however, after ENSCO was awarded the contract to operate the Transportation Technology Center. TTCI was rebranded as MxV Rail — a name that represents the “mass times velocity” formula for momentum — and relocated to a new facility 10 miles away at PuebloPlex on land from the former U.S. Army Pueblo Chemical Depot. MxV Rail’s headquarters and labs, meanwhile, relocated to the nearby Pueblo Industrial Park.
“Being able to design and build out the new FAST loop, based on more than 40 years of institutional knowledge and expertise, was a unique opportunity,” Gonzales says. “We’re grateful to all the Class I advisors and industry suppliers who helped us work through the design and construction process and make these world-class engineering capabilities available here in North America.”
While design work was under way for the new FAST loop and other test tracks, MxV Rail began moving $100 million worth of assets — including laboratory test equipment, a hodgepodge of rolling stock, and a derailment scene used to train first responders — from TTC to their new homes at PuebloPlex and the industrial park.
Phase one of FAST loop construction began in February 2023 and was substantially complete by November. The first tonnage rolled over the loop on Nov. 20. Regular test operations began on Jan. 22, 2024, kicking off a new era for FAST. The loop is the largest component of the MxV Rail Strategic Rail Initiatives Program that’s designed to improve the safety, reliability, and efficiency of the rail network.
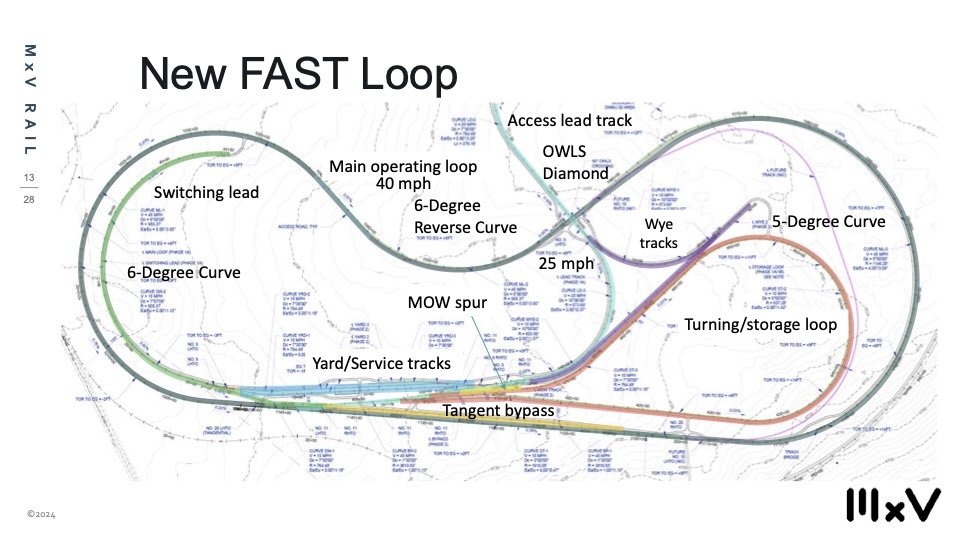
FAST Facts
Pikes Peak comes into view through the windshield every time Union Pacific SD70M No. 3886 is running clockwise and rounds the 5-degree curve at FAST’s south end. As the train enters the loop’s tangent track, four white signs pass by in Burma Shave style. Each sign marks a test section where MxV Rail evaluates different types of rail, crossties, or fastener systems, along with things like welds, rail neutral temperature, track settlement, lateral track strength, insulated joints, and bridge deck materials.
The train negotiates a 6-degree curve at the loop’s north end, enters a 6-degree reverse curve on the east side of the loop, crosses the FAST access track on a diamond, and then heads back into the 5-degree curve to begin another lap.
The old loop was cobbled together from different sections of test track and had morphed over the years. Like its predecessor, MxV Rail’s FAST loop was designed to maintain 40 mph operation while avoiding overheating the rail. Its improvements include a longer stretch of tangent track and the longer, sharper unlubricated reverse curve that increases the rate of rail wear while allowing more types of rail to be tested at any given time. FAST also is designed to be self-contained so that its operations don’t interfere with tests on MxV Rail’s other tracks: the High Speed Loop, Suspension Resonance Track, and Curving Performance Track.

The FAST loop’s access track, which links to other MxV Rail trackage as well as the outside world via BNSF Railway’s Pueblo Subdivision, features a 25-mph one-way low-speed diamond (OWLS) and a No. 11 turnout with a jump frog.
OWLS are used where a lightly trafficked line crosses a busier main line. The main line features normal rails through the diamond so that trains can operate at maximum allowable speed. Trains operating over the typical OWLS diamond on the branch line route must operate at 10 mph or below because the train rides up and over the main route’s rails in flange-bearing mode. But FAST’s is not your typical diamond. “We designed this for 25-mile-an-hour operation. We installed longer ramps on the diamond so we can test to see if we can run across it faster, which will help efficiency and safety,” Johnson explains. “If you get that crossing train across the diamond faster, you have less chance of an incident.”
A balloon track reverse loop is currently under construction to store the test train and support the once-weekly shift between clockwise and counterclockwise operation around the test track. It will allow the entire train to be turned more easily than using a wye.
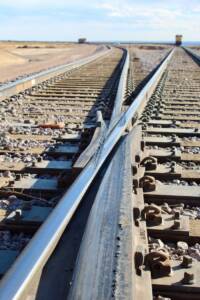
Plans are in the works to add a 1,200-foot bypass track on the FAST loop’s tangent. “The bypass allows us to put tests in that maybe can’t survive an entire night of operation. … If we’re testing something that we only need a limited amount of tonnage over, we can install it in the bypass, run over it the required amount, and then go back to the main line and not affect the other tests,” Johnson says.
The loop was built with expansion in mind, including the potential to add a switching lead, wye, and maintenance-of-way spur. Those may or may not be built depending on how MxV Rail operations develop on the new FAST track.
“We’ve been trying to phase all of our construction in a way that says ‘what’s the minimum that we need to achieve the outcomes we need?’ And then once we do that, let’s grow into it and make sure that what we’re visualizing is really necessary,” Gonzales says.
Also on the drawing board: A slower alternate route with a sharp 10-degree curve that would be tucked inside FAST’s south end. “There’s no plans to build it at this time, but if that’s what the industry decides we need, we have room for it,” Johnson says.
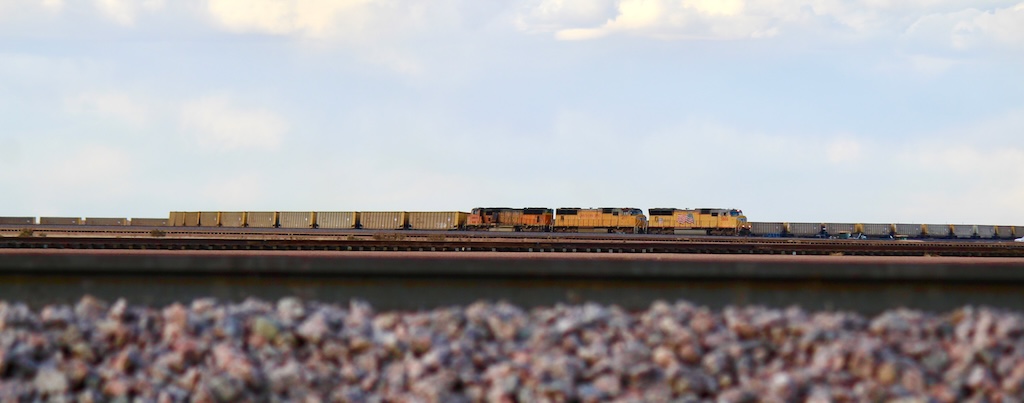
Operations Testing
The ideas for the tests under way at FAST — 28 part of the MxV Rail research program, and three involving prototypes rail suppliers have developed — come from the MxV Rail team, railroads, and suppliers. And they typically tackle problems that go beyond one railroad, one type of car, or one manufacturer.
“Safety, reliability, and efficiency are the three legs of the stool. You really can’t have a functioning, healthy North American railway system without all three of those,” says Scott Cummings, MxV Rail’s assistant vice president of research and innovation. “And so anything that we’re doing in the research program will fit into at least one of those three buckets.”
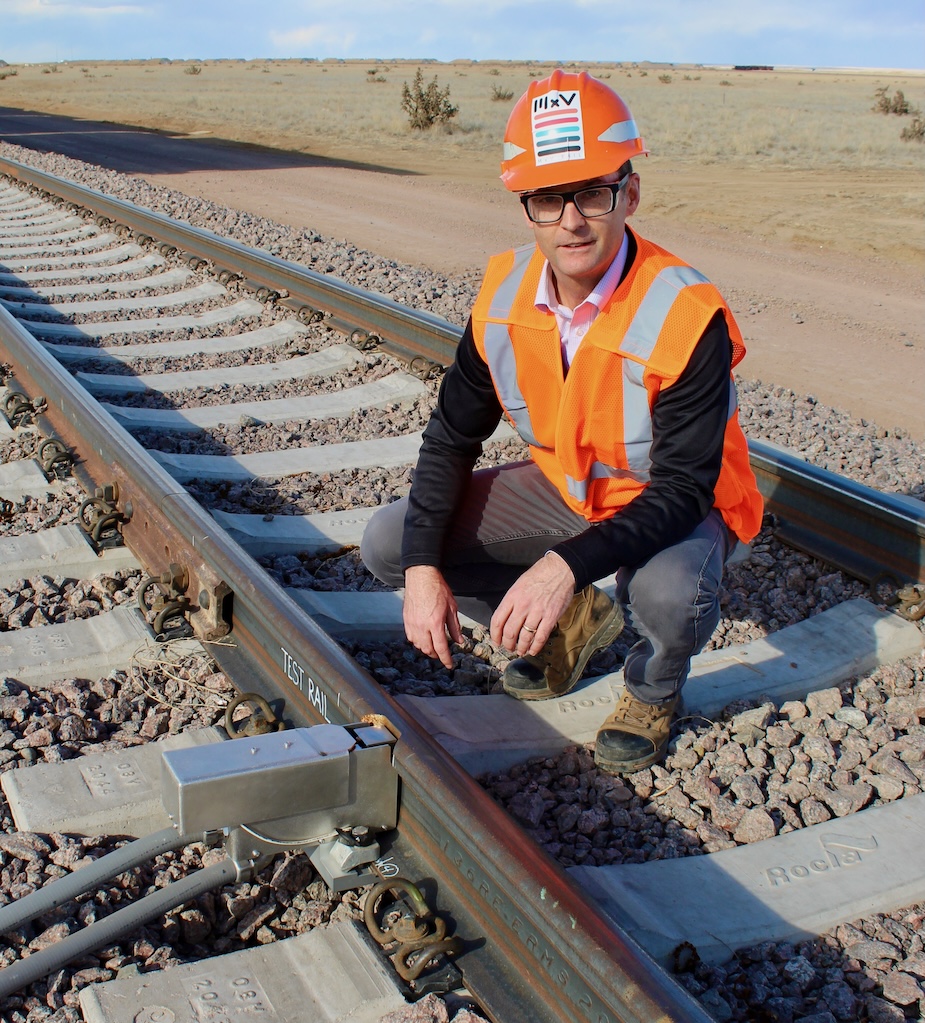
A prime example is an Innerspec Technologies, Inc. prototype cracked wheel detection system that was installed in late February. Railroads do an excellent job inspecting rail, Cummings says, but it’s a technical challenge to use non-destructive testing methods to spot cracks in wheels as they roll along at track speed in revenue service.
The ultrasonic wheel crack detector is attached to a notch cut out of the rail head. As a train approaches the detector, air pressure flings open a protective cover and raises a metal plate that makes contact with each wheel. A signal is passed through the wheel and back to the detector, which can then determine if there’s a crack in the wheel rim.
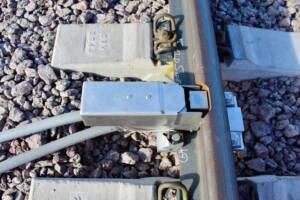
“This is something we’re excited about. It’s showing really good promise in the lab,” Cummings says while showing off the device that’s in early stages of development. “A big part of why we’re here is to kick the tires on it out here because it is way more difficult to do it in service than in the lab.”
Operations tests begin around 4 p.m. four days per week and run into the night. Why run primarily after dark? For one thing, it allows MxV Rail teams to install, remove, or adjust experiments and perform track, locomotive, and freight car maintenance during daylight hours. For another, friction created during continuous laps increases rail temperature. Running late in the day and into the overnight hours means the sun’s most direct hot rays aren’t also heating up the rails.
Before any new hardware makes its way into the loop, it first must pass testing in the MxV Rail lab. Only then will the hardware be installed and tested at FAST. If results are promising, railroads or suppliers will begin tests in revenue service. From there, a new product may go straight to commercialization or return to MxV Rail for further testing after design changes are made.
“We can do some things at FAST that you just would never want to do in revenue service,” Cummings says. “We can purposely do things to the track and then monitor them in ways that you would never want to just turn loose in the wild.”
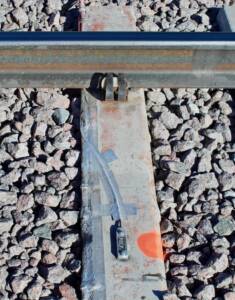
That’s not to say FAST is gambling with safety. The loop is equipped with wayside detectors that check for dragging equipment and monitor bearing and wheel temperature. It features a custom rail break detection system that includes a warning screen bolted atop the engineer’s windshield. Truck performance detectors were combined with longitudinal rail stress measurement and rail temperature readings to monitor both rail and train performance. And onboard systems monitor changes in track geometry and ride quality on every lap.
“We know exactly what’s going on with the train and the track and the components the whole time,” Johnson says. “So if there’s a safety issue or performance issue, we can identify that before it becomes a problem.”
FAST testing above the rail includes wayside detection systems that inspect wheels and bearings and monitor hot box temperature trends. Also under way: Mechanical tests on high performance wheels, constant contact side bearings, and trucks.
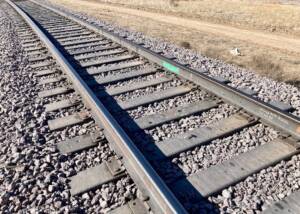
Some of the experiments — like an intermediate strength rail test begun in 2021 — were moved to the new loop so MxV Rail could continue to collect data over the long term. Seven types of rail are currently undergoing FAST testing. Under the rail sit multiple types of crossties, including different flavors of concrete ties, timber ties, and composite ties. The loop’s two-span, 62-foot bridge is unique: It sits on a curve, with one span level and the other superelevated to test bridge deck timbers and ties.
Meanwhile, back in the MxV Rail laboratory, destructive and non-destructive tests are under way on wheelsets, bearings, and rail.
“The industry support of these programs — and when I say industry, it’s the railroads, vendors, suppliers — really make this successful,” Gonzales says.
MxV Rail shares results of its research online. The goal: Provide data and science-based evaluations of track and mechanical components. Railroads and suppliers then use that data to make business decision, such as whether to install rail that’s more expensive but is proven to last longer.
MxV Rail’s 29th Annual AAR Research Review, scheduled for April 23-25, brings together technical experts from all sectors of the industry, as well as leaders from Class I and short line railroads, and suppliers from around the world. The event highlights results from the Strategic Research Initiatives Program. This year’s event will showcase current research projects via the first track walk of the FAST loop.
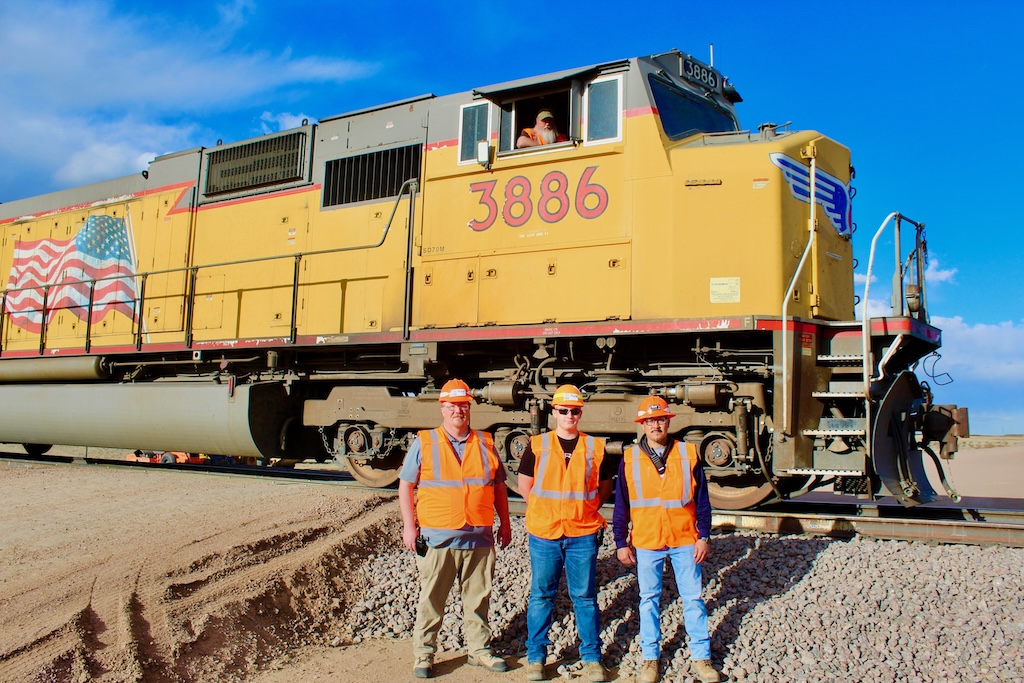
Curious if Engineer Mike gets dizzy going in circles all day
On the map, WHICH LACKS A NORTH ARROW, North is to the left.