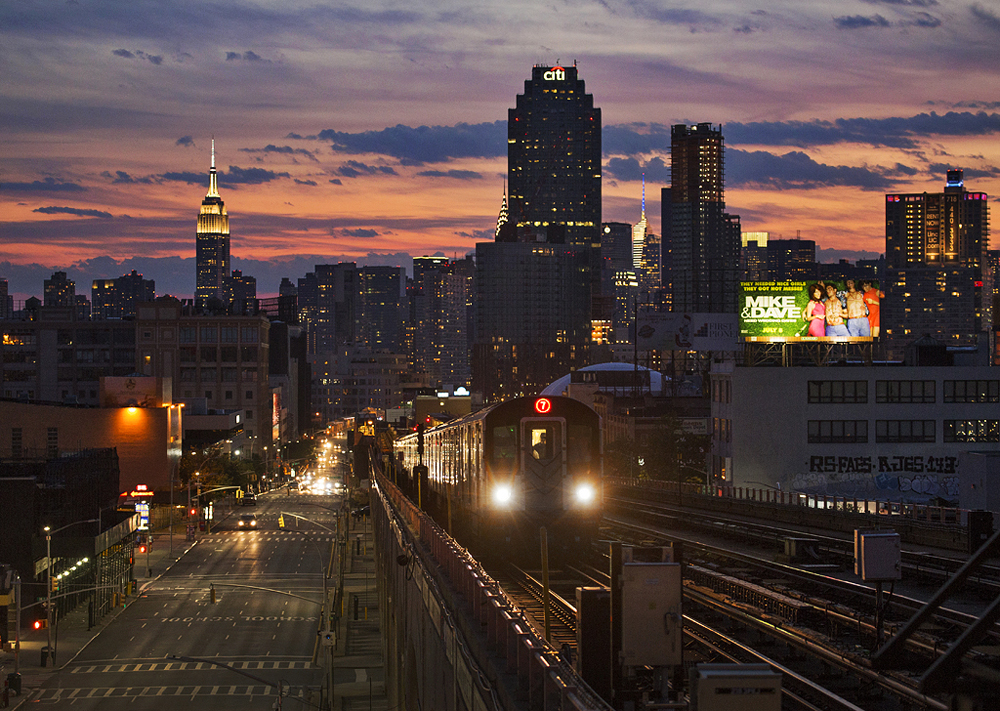
NEW YORK — Trains News Wire spoke with Metropolitan Transportation Authority Chief of Rolling Stock Tim Mulligan to discuss the agency’s robust, once-in-a-generation capital plan that involves replacing 2,000 subway cars and modernizing fleets across the agency. MTA’s five-year 2025-2029 capital plan totals $68 billion in investment, including $10.9 billion for modernized rolling stock. Mulligan is overseeing equipment procurement in this newly created role after previously serving in the agency’s Development Department where he oversaw the Construction and Development budget. The following Q&A has been edited for clarity and brevity.
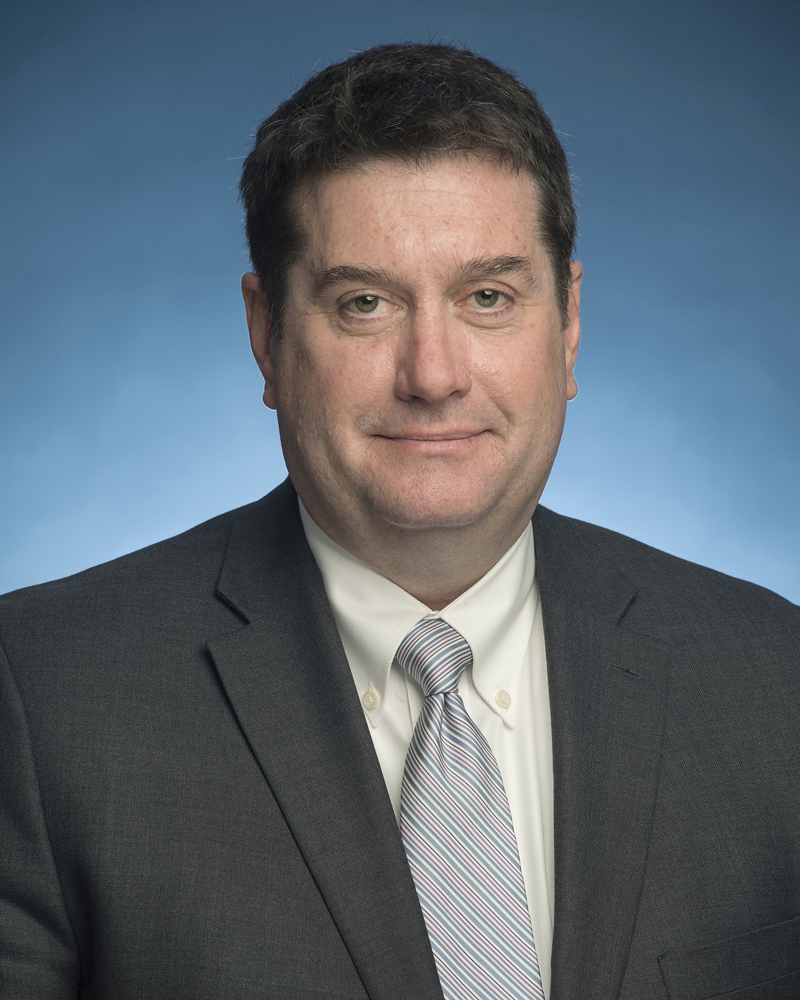
Q: How much of the current 1980s-era equipment is responsible for on-time performance issues on New York City subways?
A: Railcars typically operate at one-quarter or one-third of what the fleet average is across the different cohorts of cars that comprise the entire fleet. The performance of the cars deteriorates with time. We address that with not only inspections and regular maintenance, but also with periodic overhauls. But by the time the cars get near their end of normal life or expiration date, we see a real decline in performance and it takes a lot more effort and work to keep those cars in service. Sometimes we are able to run part of a very old fleet, but not the full complement of units we have available.
Q: What perimeters does the MTA have in procuring equipment. For example, domestic vs. foreign-supplied equipment?
A: What we are looking to do is expand competition. We have headwinds against us because of consolidation within the industry and that epicenter of the market has moved to Europe and Asia, and North America accounts for a smaller slice of the pie. We need to transition from being a big fish in a small pond in North America to the same size fish in a much larger global market.
That requires us to work harder to increase competition. We are going to do that by reducing barriers to doing business with us — looking at our certification requirements and seeing if we can make those more expedited and easier for manufacturers to prove their performance and reliability of their vehicles. We are going to be looking at modernizing the terms and conditions in our contracts so as to be more commercially fair, and we are allocating the risk more evenly between us, the manufacturers and the sub-suppliers so that we become a better owner.
We are also looking at converting our technical specifications to performance specifications, and that gives manufacturers the ability to bring more competition into the sub-supplier market when they’re looking to source who is going to supply the propulsion or the braking system or the door control system for the train.
Q: What is the agency’s current timeline for testing new equipment and entering service?
A; Rolling stock procurement is a long-term process. The procurement itself can take a long time. There’s a couple of years worth of design and then to get the pilot cars completely tested and accepted and get rolling into regular assembly line production can take five years.
That requires us to plan ahead, find solutions to work outside of the funding constraints of the five-year plan and make larger decisions and commitments and build long-term relationships with the builders for the reliability of our customers.
This is all about our customers — our customers spend more time in the rolling stock, that’s the biggest part of their commute. The stations are important. Obviously our right-of-way is important, but really the car is the major interface with the customer experience, and they deserve a safe, reliable, convenient and comfortable ride. So it’s important to us to be open to innovation, to have specifications that allow them to get the best in class service and equipment for the next several decades.
Q: Will the new equipment target greater capacity or will equipment be comparable?
A: I think it’s going to be fairly comparable. We have large-capacity vehicles and our duty cycle is very heavy — one of the most challenging duty cycles in the industry. We run so many train trips, which means we run trains closer together, and we are carrying so many passengers every day. Reliability is paramount to us. Reliability doesn’t equate to customization necessarily. We need to look at how we can standardize and increase flexibility with those performance specifications and get a quality car, and make long-term relationships that allow us to get the lowest possible pricing and leverage our size in the marketplace to guarantee stable long-term delivery cycles, so manufacturers can keep their engineers engaged and employed. When we come back in 10-15 years, we have the benefit of that educated workforce who built reliable cars for the past and can continue to design the next generation for us.
Q: So, where do things currently stand in the overall procurement process?
A: It’s a little different across the properties. We are in an active procurement for the railroads to buy additional cars to support the Madison Service into the East Side of Manhattan. The increase in Long Island Rail Road service as well as normal replacement cycles of M3s on Metro-North. We are also looking ahead to having a huge replacement need in the A-division for Transit.
More details on the agency’s five-year capital plan is available online.
Well now that Trump is going to be our President, maybe it’s time to build new manufacturing facilities here in the good old USA and bring back jobs to Americans. We know how to build freight cars and passenger cars oh and locomotives look at our past, Asia or Europe didn’t have nothing to do with our transportation System in the good old days we did it ourselves, oh and personally I think these foreign made passenger cars are UGLY and not built as strong no question about it. One final thought when we built passenger, they lasted 20-30 years, these foreign made cars only last a few years and have to be replaced and scraped, come on America and show the world how it’s done. Paul D.
All of the MTA’s trains except for one single order, the R62, have been built in the US, and all of the recent ones in NYS. Also, these trains last about 40 years. I have no idea what you mean about trains lasting only a couple of years.
Perhaps the MTA should have its own manufacturing facility…design/build for itself and contract out for customers likewise.
NY City is a different animal from the rest of the North American market. They have to buy new equipment all the time.
Everybody else, even Chicago and Toronto, buy periodically.
The vendors are accustomed to NY Specs while the other properties have to get consultants to design a car for that specific property at that specific time. There are no PCC’s or Brill Semi-convertibles.
And how many TDH-5105 or TDH-5106’s did GMC build in the 1950’s?
The vendors are not very accustomed to NY specs. Why do you think only Kawasaki and Alstom ever bid on them? What about Siemens, Stadler, Hitachi, Hyundai, CRRC, CAF? And the MTA still uses consultants to design their train cars. That’s why they had to put out an RFP for consultants to write an RFP to procure the R262s, because the MTA doesn’t have the in house capacity to even write the RFP themselves.