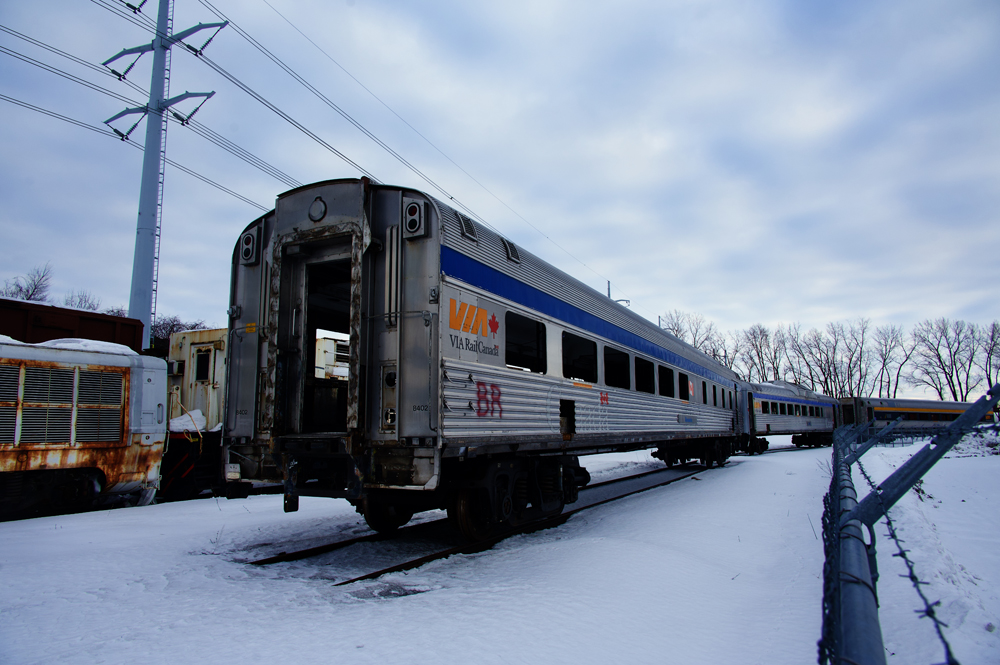
MONTREAL — Tests to determine the structural soundness of VIA Rail Canada cars manufactured by the Budd Co. from the late 1940s to mid-1950s are ongoing and formal reports have yet to be issued. However, preliminary information shared with Trains News Wire indicates that the while the cars remain fundamentally sound, corrosion may need to be addressed where trucks are attached to a car’s frame.
Based on the available information, it is unclear if this issue is widespread or serious enough to require sidelining of — or repairs to — all VIA stainless steel rolling stock. VIA has never detailed the incidents that triggered its decision to initiate a testing program.
A VIA Rail spokesperson, asked to confirm or comment on this article, wrote in an email that “some of what you have reported is not accurate. It is based on second-hand information that has been misunderstood and mischaracterized in this account.
“As you know, VIA Rail puts the safety of our passengers and employees at the centre of everything we do. VIA Rail continues to work with the Canadian rail safety regulator to proactively address structural issues with its aging stainless-steel fleet and ensure continued safe railway operations.
“As the process is still ongoing, and out of respect for the regulator, we will not be commenting publicly until our regulator (Transport Canada) has had a chance to see the engineering reports.”
Initial results
Canadian transportation analyst Greg Gormick reports that more than one person familiar with preliminary findings, though not authorized to speak publicly, has told him that all four car types tested — a Rail Diesel Car, coach, diner, and sleeping car — have withstood 800,000-pound buff strength compression tests. These tests, a fundamental requirement of crashworthiness regulations in the U.S. and Canada, are meant to show that the area occupied by passengers will remain essentially intact in the event of a collision.
“Structural integrity of the stainless steel carbody and carbon steel underframe is not the problem; corrosion at the point trucks rest on an underframe cross-member, or bolster, have raised concerns that a weakened attachment may not be strong enough to meet regulations that were not in force when the cars were built,” says Gormick.
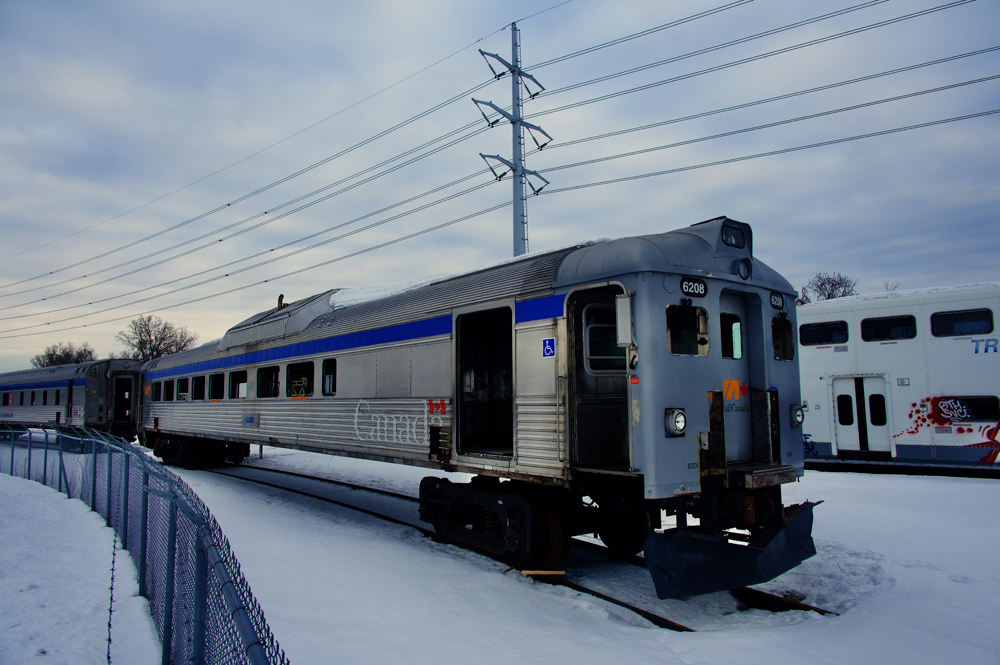
The intent of these Federal Railroad Administration safety requirements, which Canada also relies upon and which have been revised since the cars were manufactured, is to make sure the passenger car’s wheelset stays with the frame during a derailment.
According to Gormick, extensive carbon steel carbody corrosion was the main reason VIA jettisoned all of its former Canadian National lightweight, non-stainless steel passenger cars when the company went through a budget-induced contraction in the 1990s. Originally constructed by Canadian Car & Foundry in the mid-1950s, many of the ex-CN coaches have undergone top-to-bottom rebuilds by three manufacturers and now are Rocky Mountaineer SilverLeaf glass-topped sightseeing cars.
Corrosion not widespread
The owner of the company VIA chose to structurally reconfigure eight Budd-built Chateau sleeping cars and four Park dome observation cars is skeptical of the reported findings, based on her extensive experience over three decades with that and other rebuild projects, including transforming SilverLeafs.
June Garland, president of Milwaukee-based Avalon Rail, Inc., made the decision to close her passenger car repair business in 2019. She tells News Wire that during her time in the industry, she saw only one instance of record involving bolster corrosion, and that occurred with another railroad’s equipment. Avalon encountered no corrosion issues of note when it rebuilt trucks on VIA, Rocky Mountaineer, Union Pacific, and privately owned railcars constructed from the late 1940s to early 1960s.
“Potential truck parts availability and bolster issues were discussed as we were working on the Union Pacific business train car fleet, although corrosion problems were not an issue as trucks were disassembled and rebuilt,” Garland says.
She points out that defects such as cracks in the stainless steel side sills, as well as gouges, nicks, and abrasions, can be corrected.
“Attachment points for any dissimilar metal is always a concern throughout stainless steel as well as carbon steel cars, but bolsters and trucks are both carbon steel, not stainless,” Garland says, adding, “True ‘corrosion,’ in my experience, is not generally found with truck bolsters.”
Parts can be custom fabricated as needed with the exception of newly cast bolsters, “which were problematic for UP and others to source,” Garland recalls, “so replacing bolsters would be difficult; a manufacturer would have to be selected that was willing to take on the project.”
Mitigation potential
VIA’s stainless steel passenger cars and handful of RDCs comprise North America’s last remaining post-World War II streamliner fleet. The Toronto-Vancouver, British Columbia, Canadian can’t exist without them; neither can the Montreal-Halifax, Nova Scotia Ocean, remote service trains, and current Quebec City-Windsor, Ont., corridor operations. The company is only in the earliest stages of a replacement program for this equipment [see “VIA joins Amtrak in attempting to replace long-distance passenger cars,” News Wire, Jan. 30, 2023].
When questions arose last fall about the cars’ structural integrity, VIA began adding unoccupied buffer cars as a precaution to protect passengers in the event of a collision [see “VIA: Need for ‘in depth’ inspections …,” News Wire, Oct. 19, 2022]. But if the cars have passed the compression tests, and therefore continue to meet their designed horizontal buff strength capability, that mitigation may no longer be needed.
It is possible that a “fix” can be devised that satisfies safety requirements to keep trucks from separating from carbodies. Such updates or revisions are often developed to allow freight and passenger rolling stock to continue to operate when new regulations might otherwise lead them to be retired.
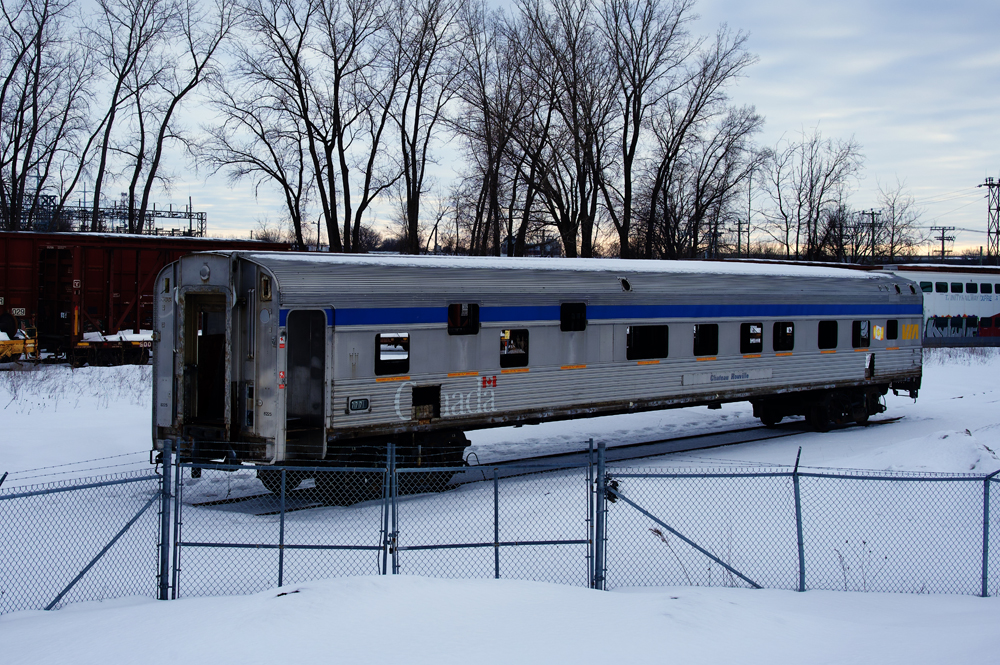
This equipment is over 60 yrs old nothing lasts forever, either replace it or forget it!
So hard to prove that something is safe.
S@#T happens and so Engineers test to find the breaking point of materials. Then the worrywarts want MORE strength designed in to the product. Taken to the limits, you get a foam lined barrel that you can use to survive going over Niagra Falls in.
Really, they’re worried about the trucks “POSSIBLY” separating from the carbody…as if that poses a great danger to anyone on the train itself.
The three fatalities in DuPont, Washington, were from a separated wheelset crashing through the wall of the car during the derailment: NTSB/RAR-19/01. So, yes, this is a hot button topic.