Train handling
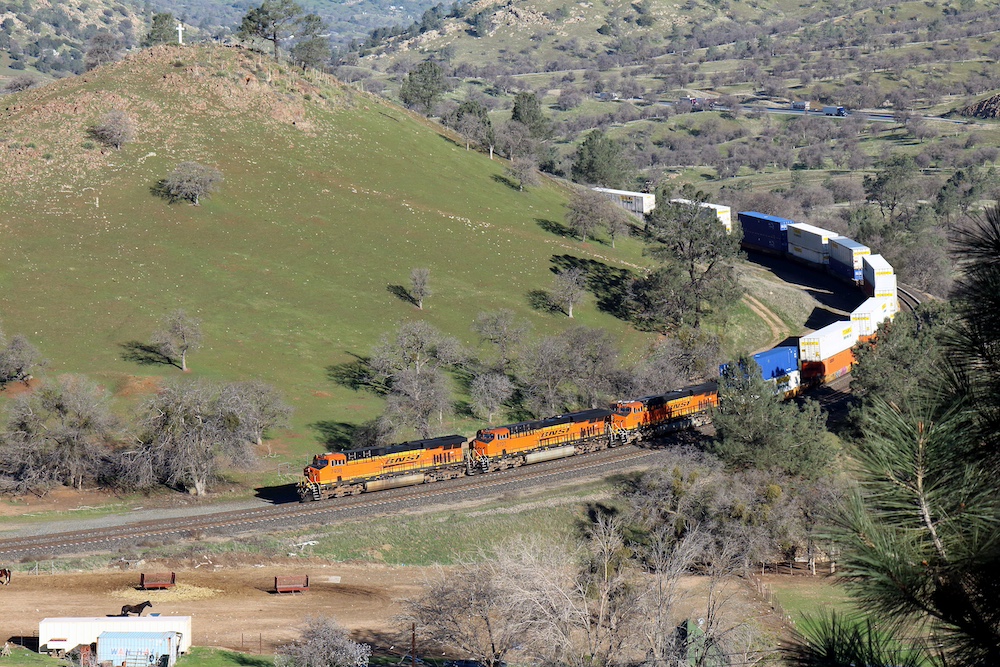
The United States Bureau of Labor Statistics estimates there are more than 36,000 locomotive engineers in the United States. Whether it’s an older Geep switching cars in an industry, a passenger train racing across the country, or a Class I freight on the main line, the techniques that engineers learn and have at their disposal are pretty much the same throughout the craft, no matter the size or age of the power or the length of the train. Let’s look at the science of train handling.
Knowledge
The first and most important part of train handling is territory knowledge. Engineers must have a working knowledge and get annual check rides on the section of the railroad they will be working on. Engineers need to spend enough time in the seat, operating over the territory to learn its physical characteristics. These characteristics such as grades, curves, bridges, crossings, speed limits, switches, signals, and derails are important things that an engineer must know to help make decisions when operating the train.
Train’s makeup
Secondly, an engineer needs to know the train’s makeup.
Part of the briefing with the conductor or previous crew will help determine the following:
- How many units are on the train and if any of them are distributed power.
- How many loaded and empty cars there are on the train.
- How the units are placed in the train.
- If there are any cars with special restrictions — a high and wide load or close clearance car.
Once an engineer knows how the train is made up, he or she can use different methods of train control to ensure good train handling.
Methods of train control
The methods of train control will depend on the territory. For example, an engineer going downgrade that leads into a bowl and then into an uphill grade may know that they could leave the train to coast as the momentum will carry them up the next hill because too much air would stall out the train as it starts its climb. An engineer’s goal is to keep the slack controlled between the cars and engines to prevent buff or stretch forces on the couplers — too much of either can lead to a derailment.
Throttle modulation is one of the simplest forms of train control. Manipulating the throttle one notch at a time (either up or down) can help keep the train at a constant speed. If the engineer needs to lose a little speed while the train is going up a slight grade, notch down by one may be all that is needed to slow down a train and then notching right back up to keep the momentum. Or the opposite can be true if there is a slight grade up, the engineer may notch up by one or two and increase speed before backing off the throttle.
While rolling along, if the engineer wants to keep their throttle position, but they’re still gaining too much speed, he or she can use short cycle braking.
Short cycle braking is the method of placing the automatic brake into the minimum set position, bailing off the independent, thereby letting the air out of the train line for a few seconds which starts to place a small set on the train brakes. Before allowing the brakes to grab too much resulting in stalling out, the engineer places the automatic brake back into release allowing the train to continue rolling at the desired speed.
Power braking is used to help bring a train to a desired stop while still using throttle. This can be used pulling or shoving the train. In this method, the engineer places a small set, they may start at a minimum set and then take more air as needed, bail off the independent and keep the throttle notched out. Engineers I’ve talked to over the years say that this is the hardest form of train control to master. It takes practice to feel what the train is doing. An engineer needs to make sure there is enough air being taken while balancing the amount of power being added in order to not stall out before the stop.
Dynamic braking is the last thing. Dynamic brakes help prevent wear and tear on friction-based brakes. Most dynamic brakes are rheostatic which means the large amounts of electric energy from the traction motors are dissipated through the electrical grid that is kept cool with large cooling fans.
To use the dynamic brakes the engineer must:
- Return the throttle to idle and wait approximately 10 seconds.
- Move the dynamic brake handle to the Set Up position and wait as the cooling fans start spinning.
- Then, move the handle slowly to find the desired amount of braking — moving it up or down as needed.
Dynamic brakes are great for traveling down mountain grades where an engineer wouldn’t want to burn up the normal brakes.
Conclusion
This is not an exhaustive list, as it also doesn’t consider the type of brake stands, an engineer’s experience, or passenger trains that can have a graduated release.
Engineers must spend many hours in the seat before they can be signed off and receive their Part 240 certification. By the time engineers receive their cards, they will have the confidence that they can use these techniques to keep trains running smoothly and avoid unnecessary delays.
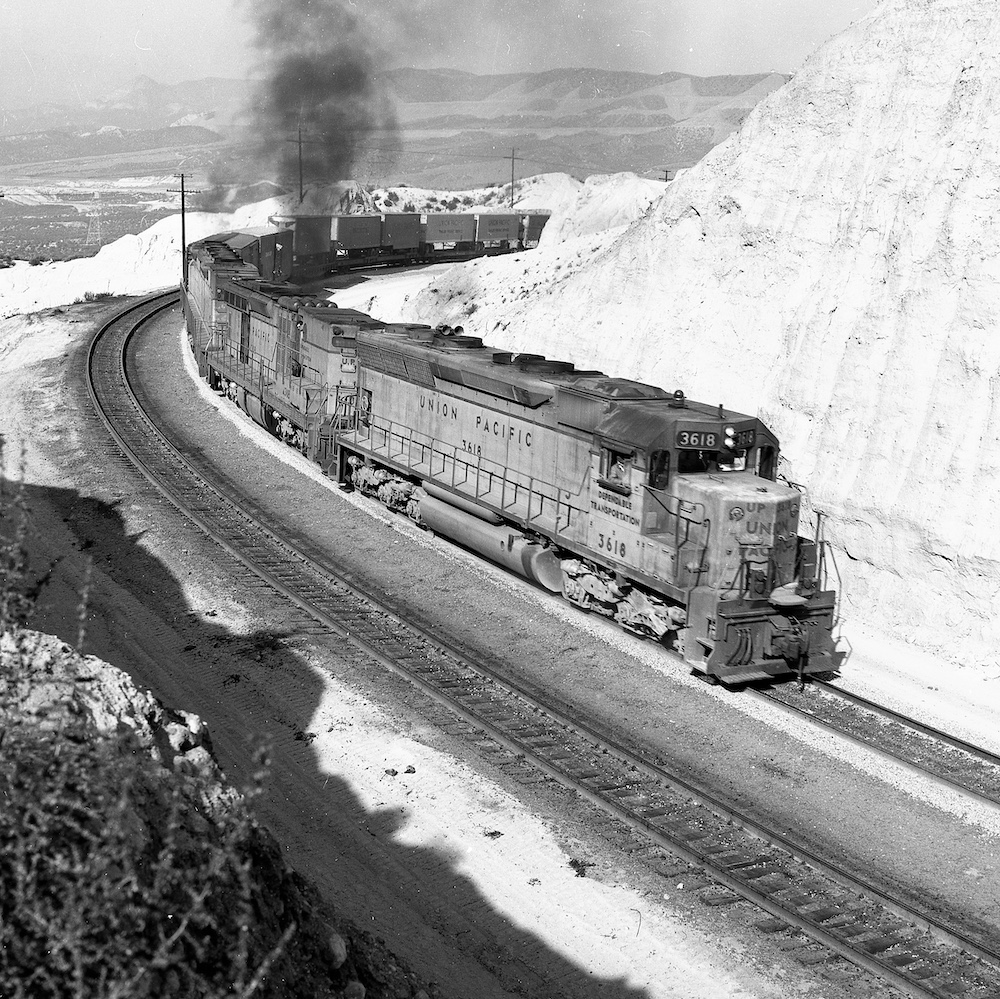