Intermodal equipment
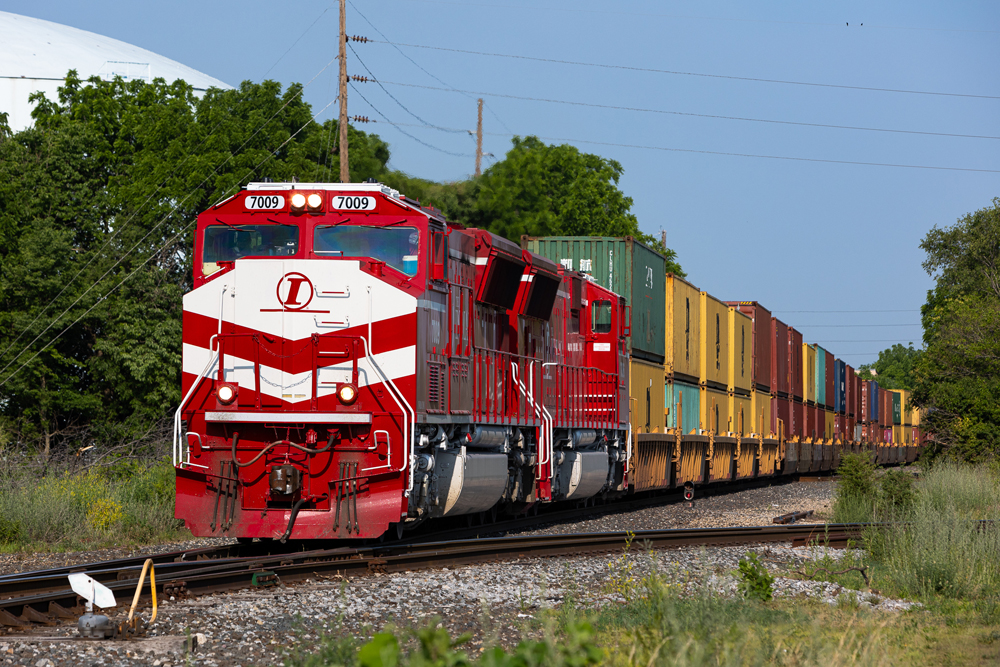
If you’re trackside, odds are you’re going to see an intermodal train. Intermodal made up 49% of the 34 million units of freight carried by U.S. railroads last year, more than four times higher than coal, the next largest commodity.
Odds are that intermodal train will mostly have railcars owned by TTX, a railcar pooling company owned by all Class I railroads, whose fleet includes more than 140,000 cars hauling intermodal or automobile traffic. TTX cars are recognizable by their yellow paint and reporting marks that begin with “TT.” Individual railroads (most notably BNSF) also own intermodal cars, but their fleet size pales in comparison to TTX.
On the other hand, the vast majority of the tens of millions of containers and trailers are owned by entities other than railroads, usually their customers. Ocean shipping lines, trucking companies, and third-party leasing companies dominate ownership of “boxes” — as trailers and containers in intermodal service are called.
Trailers
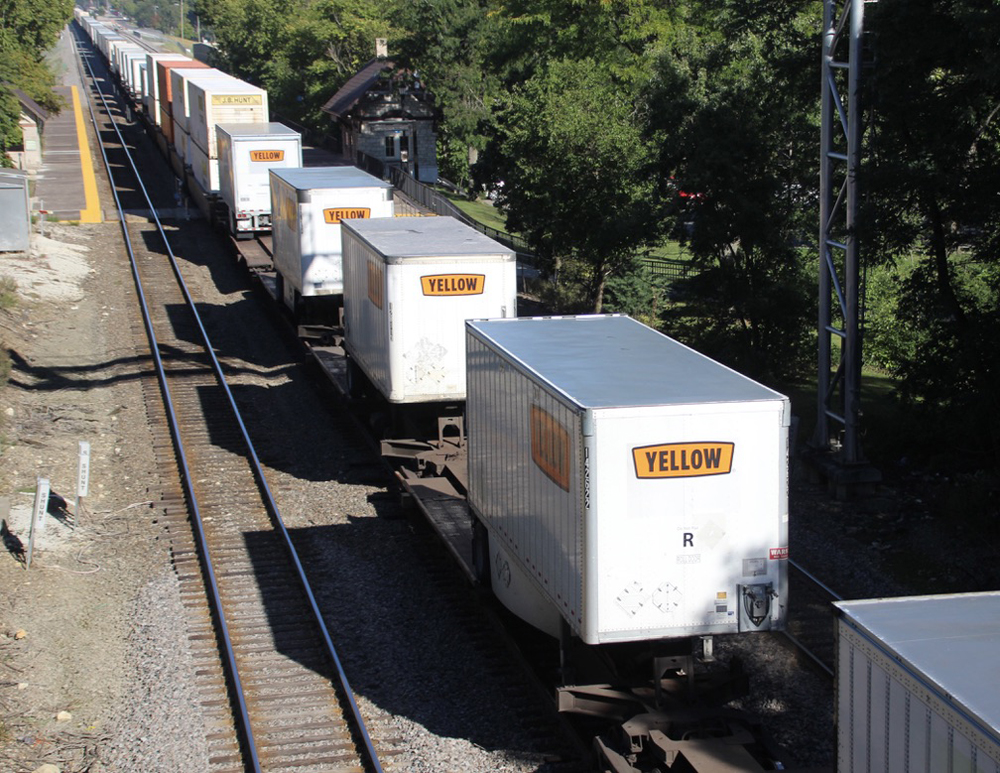
Intermodal service started with trailers on flatcars (TOFC) back in 1936. Traditionally, trailers built for rail service had to be constructed to sturdier specifications than highway trailers. Heavier construction was necessary to contain load shifts due to slack action or impacts with other cars in switching operations — forces not normally experienced in highway service. Of course, these trailers weighed more than highway trailers, which reduced the amount of payload it could carry but cost more.
Today, the modifications are more minor (reinforcement at key points and lift pads) since intermodal trains use mostly articulated equipment that reduced slack action and shocks to the trailers.
Trailers differ mainly in length and width — both dimensions are influenced by a mass of federal and state laws that regulate vehicle size and weight. The growth of the typical piggyback trailer from 35 feet in length during the 1950s to 40 feet in the 1960s and ’70s to 45 feet in the 1980s, tracked the steady liberalization of state restrictions on truck size.
Today, the most common trailer length are 28 feet or 53 feet. The 28-foot units have a single axle and are favored by United Parcel Service and less-than-truckload (LTL) carriers, which hook them together in two-unit combinations (or three-unit combinations where state law allows) for highway operation. Hot intermodal trains carrying premium traffic often have 28-foot trailers in its consist.
Fifty-three-foot trailers mimic the standard truck size and have replaced the traditional 45-foot railroad-supplied trailer: two 45-footers are the largest pair that can be loaded on the standard 89-foot intermodal flatcar.
Trailers with level floors and no heaters or refrigerators (known as “dry vans”) predominate. “Reefer” units have diesel-powered heating and cooling units for temperature-sensitive cargo. “Flatbed” trailers, like flatcars, haul loads that do not need protection from the weather.
But trailers make up a shrinking portion of the intermodal market — now less than 10% of intermodal movements. Many have predicted the imminent demise of intermodal trailer service, but as long as UPS and other large customers keep demanding the service, especially in dense lanes like Los Angeles — Chicago or Chicago to the east coast.
Containers
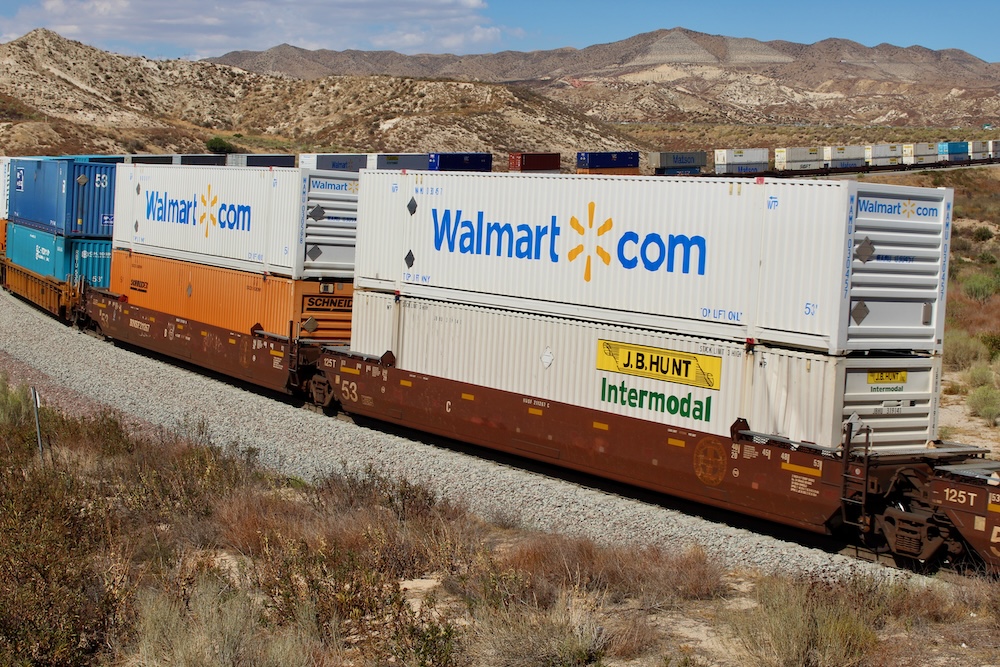
Intermodal began with trailers because the basic trailer design had become accepted in the marketplace and “circus loading” of trailers required minimal investment in terminals. In the 1950s, however, trucker Malcolm McLean developed the concept of the intermodal container: a steel box that could be moved from ship to rail to truck without unloading.
While the container concept was briefly embraced by a few railroads during the 1960s, it did not take off until shipping lines pioneered “land-bridge” rail services across the U.S. and rail clearances were expanded to handle double-stacked containers.
Today, containers have supplanted trailers as the intermodal box of choice. Double-stacking drove this decision because two containers can be hauled in the space of one trailer, just higher. Precision Scheduled Railroading’s emphasis on fewer but longer trains has put a premium on space-in-train, further advantaging double-stacked containers over trailers.
Intermodal containers come in two basic flavors — international and domestic.
Containers built for international service must conform to design and length standards established by the International Standards Organization (ISO). This enables ocean carriers to stack them together on ships, or railroads to load them on flatcars, regardless of ownership or country of origin. International containers are usually either 20 or 40 feet long. The shorter 20-foot boxes generally will carry heavy-loading commodities, such as machinery or fasteners (nuts, bolts, screws, washers), in deference to crane capacities and highway load limits, while lighter goods travel in the more-common 40-foot boxes. International containers are usually owned by individual shipping lines or consortium — the pink containers of ONE (Ocean Network Express based in Japan) are very distinctive. The international containers you see on trains usually have an ocean voyage connected with their rail journey.
Domestic containers — more than 300,000 in North America — are usually 53 feet long, designed to take advantage of the maximum lengths allowed on U.S. highways, and have the same capacity as a regular truckload. Truck lines (such as J.B. Hunt and Schneider) provide most of the domestic containers used in intermodal service, while logistics company Hub Group has 50,000 of its own boxes. Railroads supplement these containers with its own jointly-owned pools of containers — the EMP and UMAX pools total about 50,000 containers. International freight in 40-foot boxes is often “restuffed” into 53-foot containers for domestic movements at coastal warehouses before moving inland.
Waste hauling is an interesting rail container niche. Sludge or dirt is often carried in specialized half-height 20-foot containers, while old 40-foot international containers can be converted to carry trash or debris by having their roofs removed. If you see a set of international double-stacks in an unexpected place and if they have tarps instead of solid roofs, the containers are likely headed for a landfill.
Loading containers on railcars is harder than it looks. Not only must the length of each box be considered, but also its configuration and weight and the carrying capacity of the railroad cars, which can vary. A pair of 20-foot containers, for example, may weigh enough to load one well to its capacity, while the next well may be under capacity with a 53-foot container of down coats on top of a 48-foot container of toys.
Chassis are the removable wheels and frames that are used to ferry containers between rail terminals and customers or in many cases ocean carriers. These come in lengths that correspond either standard box lengths, and many can adjust to take containers of different lengths. One of the most difficult tasks in intermodal transportation is distributing chassis to ensure there are enough at each terminal to handle the available business, but not too many. If too many chassis accumulate in one terminal, they will be stacked and shipped by rail to a location where chassis are needed.
As intermodal boxes evolved, so did intermodal railcars. Railroads haul intermodal equipment in two types of cars: flatcars and well cars.
Flatcars
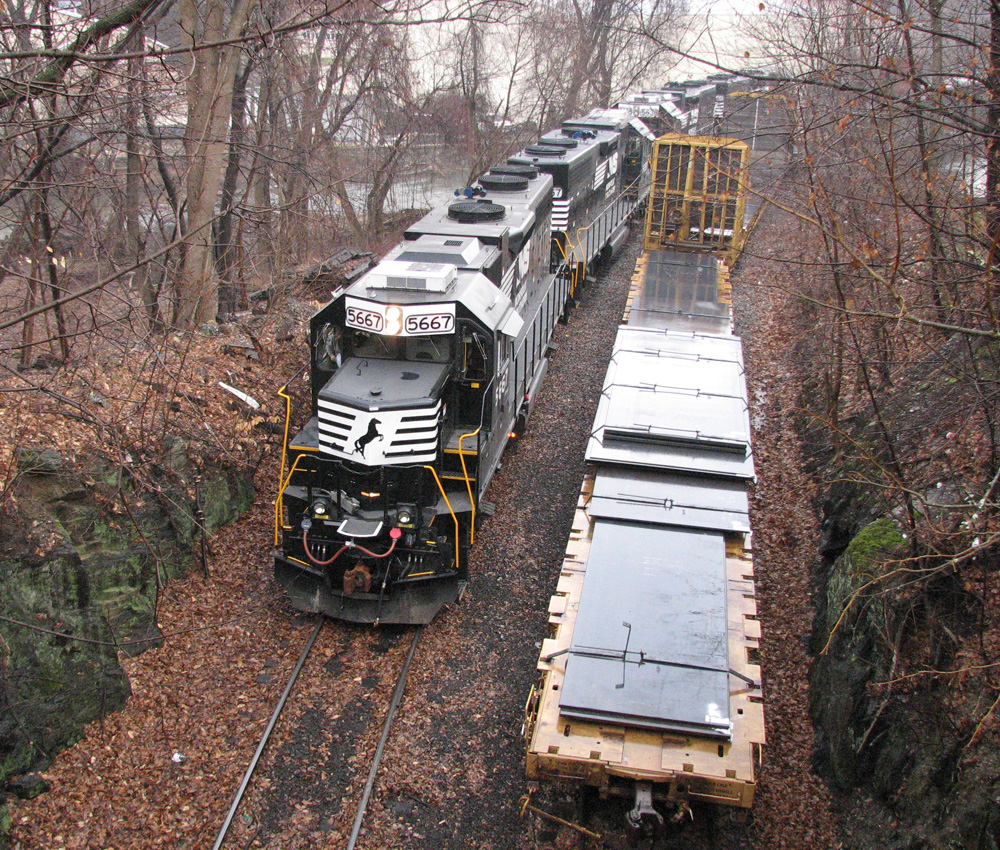
For twenty years after its introduction in 1961, the 89-foot flatcar was the workhorse of the intermodal freight-car fleet. Carrying two standard 40-foot trailers or its container equivalents, the 89-foot car was well suited to the railroads’ needs — that is, until the state and federal governments began increasing the maximum length of trailers permitted on the highways. As trailers and containers have grown longer and wider, railroads, car owners, and car builders serving the intermodal market had to scramble to keep up, accounting for the various types of equipment seen today.
Many 89-foot flatcars (or “pigs,” for their role in piggyback service) are still in service, but most of the survivors have been re-equipped with auto racks to carry cars and trucks. Some railroads — like Chicago & North Western, Santa Fe, and Norfolk Southern — converted excess 50-foot boxcars and 100-ton bulkhead flatcars to handle 45-foot and 48-foot trailers during the early 1980s. However, these efforts resulted in “lead sleds” that were heavier, and thus less efficient, than half of an 89-foot flatcar.
But to satisfy customer demand for better ride quality, as well as the railroads’ desire to reduce maintenance costs and tare weight (thus fuel consumption), the industry turned to articulated “spine cars.” Articulated intermodal cars — that is, cars with separate load-bearing units resting on common trucks — were initially developed by the Santa Fe in the late 1970s. By eliminating several sets of trucks and couplers, and reducing the carbody to a steel center sill with hitches and wheel supports, the “spine car” design both saved weight and reduced slack action, providing a smoother ride.
Contemporary spine cars are capable of handling trailers or containers up to 53 feet long, most commonly in a five-platform configuration. Because of the need to reposition equipment or an imbalance in the number of trailers vs. containers on a train, spine cars are sometimes used to handle containers. Unfortunately, this practice precludes the favorable economics of double-stacking.
Well cars
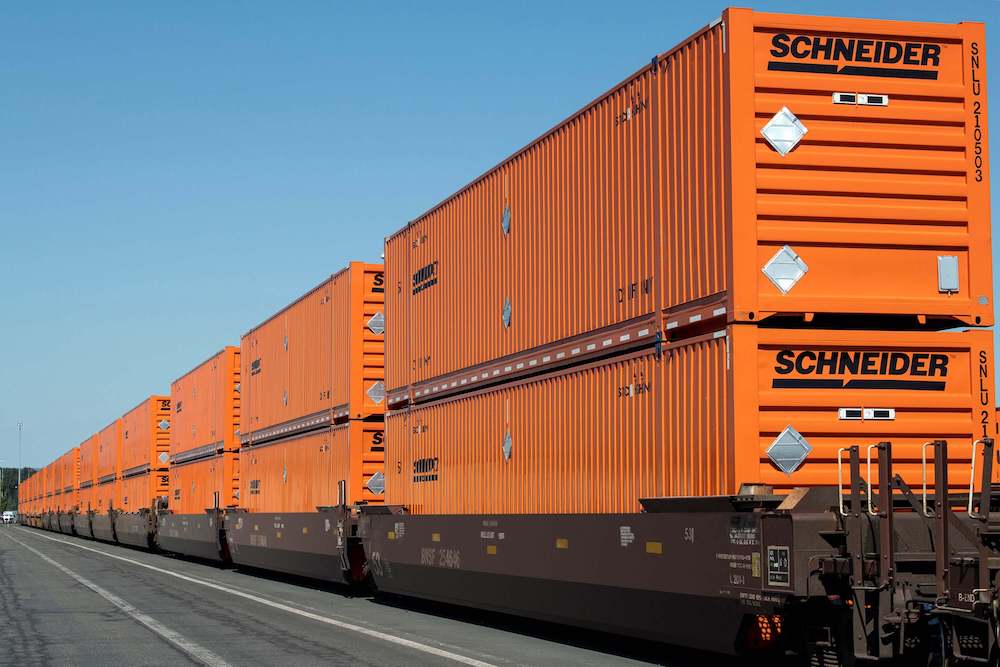
When Southern Pacific and Sea-Land pioneered double-stacking containers in the late 1970s, a new kind of intermodal railcar was required. The well car was born, named for how containers are positioned as low as possible in “wells” in order to be double-stacked. Well car usage greatly expanded in 1984 when ocean shipper American President Lines developed a network of stack trains spanning the continent and railroads increased clearances to handle that business.
These double-stack cars combine the ride-enhancing qualities of articulation with the efficiency inherent in transporting containers two-high. They permit railroads to carry containers, which had historically generated low yields, in profitable quantities.
Early double-stack well cars employed bulkheads to secure the top row of containers, but the bulkheads added extra weight to the car and limited the use of upper wells to handle larger containers. Instead, cars built since the mid-1980s don’t have bulkheads and rely on interbox connectors to hold the containers in place, just as on ships.
At first wells were uniformly sized for 40-foot international containers, but subsequently, cars with wells for larger containers were developed as domestic containers came into use.
Today, the most common well-car configuration are 5-platform cars with 40-fo0t wells or three-platform cars with 53-foot wells. Of course, 40-foot containers can fit in the larger wells, and interestingly, larger containers often ride on top of smaller containers. Some “all purpose” well cars have hitches so that trailers can be handled in well cars if needed.
In all their variations, well cars have become the intermodal standard car.
Other types of intermodal equipment
As railroads have tried to convert freight from road to rail using intermodal, they have often tried innovative equipment designs.
The latest is a self-propelled battery-operated rail vehicle from Parallel Systems, which would move intermodal boxes — singly or in multiple — autonomously along rail lines. Shortline holding company Genessee & Wyoming has applied to test Parallel’s technology on its lines in Georgia.
Triple Crown Services, a subsidiary of Norfolk Southern, is the last user of RoadRailer intermodal equipment, which dispenses with cars altogether to reduce terminal costs. RoadRailer service is down to a single pair of trains daily between Detroit and Kansas City, and is expected to be converted to containers within the next few years. Even Amtrak ran RoadRailers as part of its passenger trains for a time as part of its aborted mail and express initiative.
Canadian Pacific used the “Iron Highway,” a double-ended trainset that split in the middle to permit circus-style unloading of trailers at terminals without expensive terminal investments. CP’s service, branded “Expressway” ran in Ontario and Quebec from 2000 until 2018.
“Intermodal service started with trailers on flatcars (TOFC) back in 1936.”
This just plain wrong!
The integration of motor freight and rail freight service (Intermodal) started in the early 1920’s. Using containers! The early 1920’s were about as soon as a motor truck that could haul a decent amount of freight became available. The New York Central kicked things off.
This early container system provided improved service to customers at lower charges. At the same time it improved railroad profitability because it was a more efficient method of moving freight.
So, naturally, the government regulators had to put a stop to it. In 1931 the railroads were ordered to raise the container charges to non competitive levels and much of the freight started a mass diversion to trucking.
The government kept its dead hand on intermodal development for 50 years.
This article showed how railroads have used different types of equipment to try and serve various users of intermodal service. However I still feel they loose out on too many chances to add to their traffic by only trying to serve the longer haul trips. Planned and scheduled correctly they could expand this service to shorter trips and still earn a decent return on investment.
Very interesting article. Great information.